Product Name | Carbon Steel Pipe/Boiler Steel Pipe |
Material | A53 GrB,A36,ST52,ST35,ST42,ST45,X42,X46,X52,X60,X65,X70 |
Standard | API 5L,ASTM A106 Gr.B,ASTM A53 Gr.B,ASTMA179/A192,ASTM A335 P9,ASTM A210,ASTM A333 |
Certificates | API 5L,ISO9001,SGS,BV,CCIC |
Outer Diameter | 13.7mm-762mm |
Wall Thickness | SCH10,SCH20,SCH30,STD,SCH40,SCH60,SCH80,SCH100,SCH120,SCH160,XS,XXS |
Length | 1m,4m,6m,8m,12m according to buyer's request |
Surface Treatment | black paint,varnish,oil,galvanized,anti-corrosion coated |
Marking | Standard marking,or according to your request.Marking Method:Spray white paint |
End Treatment | Plain End/Bevelled End/Grooved End/Threaded End With Plastic Caps |
Technique | Hot Rolled or Cold Rolled ERW |
Package | Loose package;Packaged in bundles(2Ton Max);bundled pipes with slings at the both end for easy loading and discharging;wooden cases;waterproof woven bag |
Test | Chemical Component Analysis,Mechanical Properties, Technical Properties, Exterior Size Inspection,hydraulic testing,X-ray Test |
Application | Liquid delivery,structure pipe,construction,petroleum cracking,oil pipe,gas pipe |
API 5L X42-X80, PSL1&PSL2 Oil and Gas Carbon Seamless Steel Pipe is used for conveying gas,water,and petroleum of both the oil and natural gas industries.
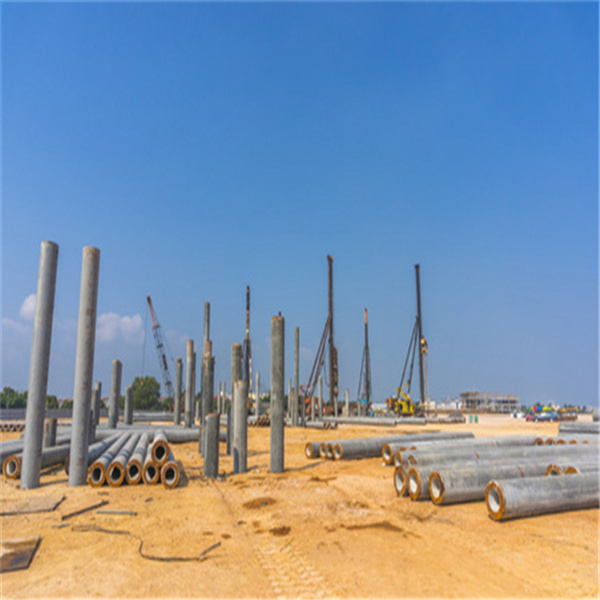
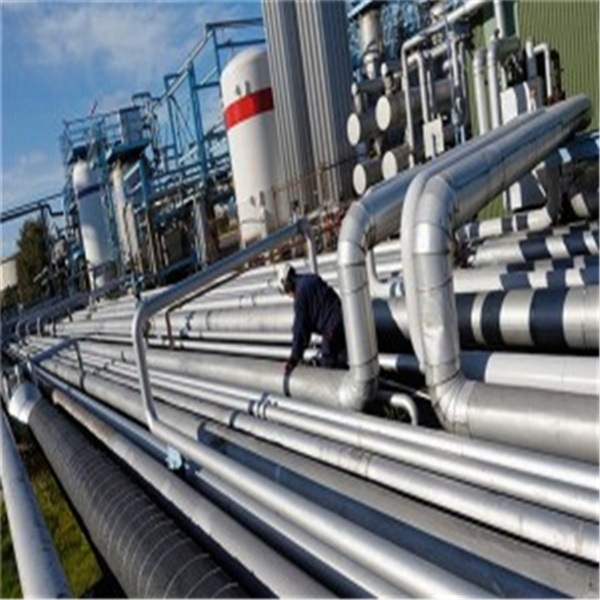
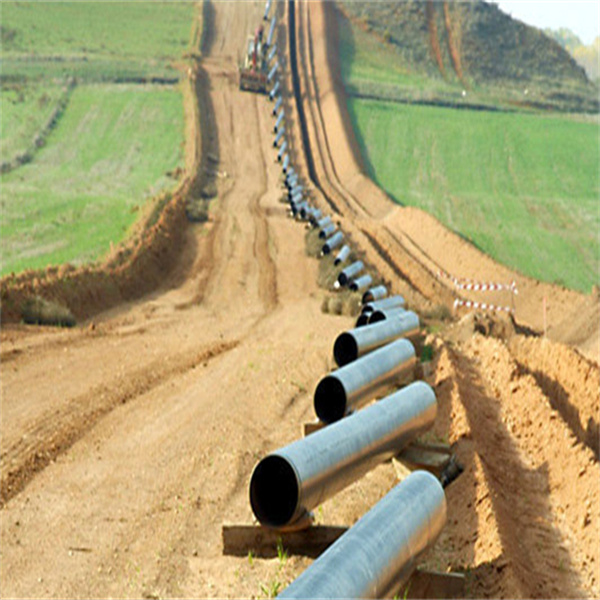
API 5L X42-X80, PSL1&PSL2 Oil and Gas Carbon Seamless Steel Pipe are made either by cold-drawn or hot rolled, as required by the customers.
API 5L X52 PSL1&PSL2 Oil and Gas Carbon Seamless Steel Pipe are made either by cold-drawn or hot rolled, normally small sizes ones by cold-drawn and big sizes by hot rolled.
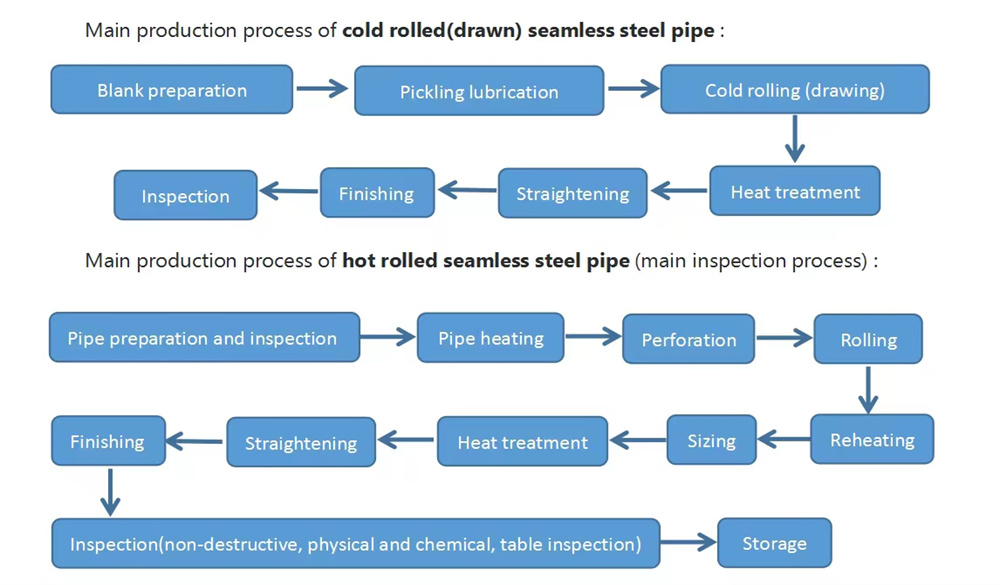
Grade and Chemical Composition (%) For API 5L PSL1
Standard |
Grade |
Chemical composition(%) |
|||
C |
Mn |
P |
S |
||
API 5L |
X42 |
≤0.28 |
≤1.30 |
≤0.030 |
≤0.030 |
X46,X52,X56 |
≤0.28 |
≤1.40 |
≤0.030 |
≤0.030 |
|
X60,X65 |
≤0.28 |
≤1.40 |
≤0.030 |
≤0.030 |
|
X70 |
≤0.28 |
≤1.40 |
≤0.030 |
≤0.030 |
|
X52 |
≤0.28 |
≤1.40 |
≤0.030 |
≤0.030 |
Grade and Chemical Composition (%) For API 5L PSL2
Standard |
Grade |
Chemical composition(%) |
|||
C |
Mn |
P |
S |
||
API 5L |
X42 |
≤0.24 |
≤1.30 |
≤0.025 |
≤0.015 |
X46,X52,X56 |
≤0.24 |
≤1.40 |
≤0.025 |
≤0.015 |
|
X60,X65 |
≤0.24 |
≤1.40 |
≤0.025 |
≤0.015 |
|
X70,X80 |
≤0.24 |
≤1.40 |
≤0.025 |
≤0.015 |
|
X52 |
≤0.24 |
≤1.40 |
≤0.025 |
≤0.015 |
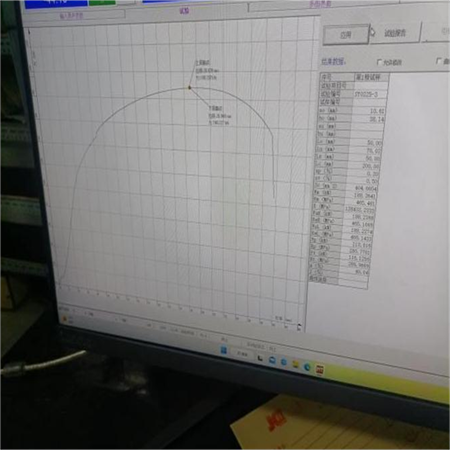
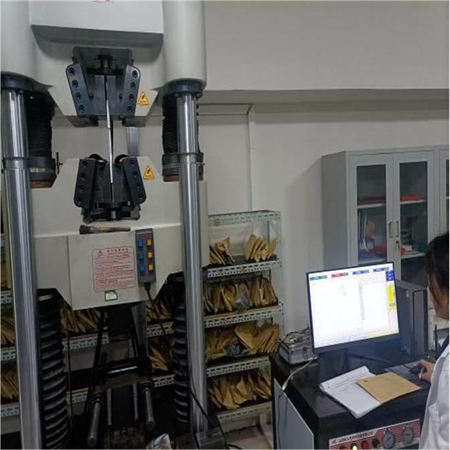
Mechanical Properties of API 5L GR.B X42-X80/X52 (PSL1):
Grade |
Yield Strength(MPa) |
Tensile Strength(MPa) |
Elongation A% |
||
|
psi |
MPa |
psi |
MPa |
Elongation (Min ) |
X42 |
42,000 |
290 |
60,000 |
414 |
21~27 |
X46 |
46,000 |
317 |
63,000 |
434 |
20~26 |
X52 |
52,000 |
359 |
66,000 |
455 |
20~24 |
X56 |
56,000 |
386 |
71,000 |
490 |
|
X60 |
60,000 |
414 |
75,000 |
517 |
|
X65 |
65,000 |
448 |
77,000 |
531 |
|
X70 |
70,000 |
483 |
82,000 |
565 |
|
X52 |
52,000 |
359 |
66,000 |
455 |
20~24 |
Mechanical Properties of API 5L/X52 GR.B Seamless Line Pipe (PSL2):
Grade |
Yield Strength(MPa) |
Tensile Strength(MPa) |
Elongation A% |
Impact (J) |
||
|
psi |
MPa |
psi |
MPa |
Elongation (Min ) |
Min |
X42 |
290 |
496 |
414 |
758 |
21~27 |
41(27) |
X46 |
317 |
524 |
434 |
758 |
20~26 |
41(27) |
X52 |
359 |
531 |
455 |
758 |
20~24 |
41(27) |
X56 |
386 |
544 |
490 |
758 |
|
|
X60 |
414 |
565 |
517 |
758 |
|
|
X65 |
448 |
600 |
531 |
758 |
|
|
X70 |
483 |
621 |
565 |
758 |
|
|
X80 |
552 |
690 |
621 |
827 |
|
|
X52 |
359 |
531 |
455 |
758 |
20~24 |
41(27) |
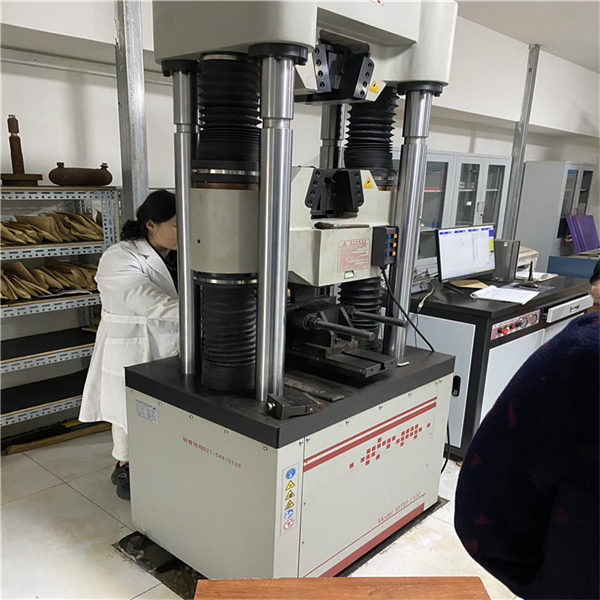
Mechanical Testing
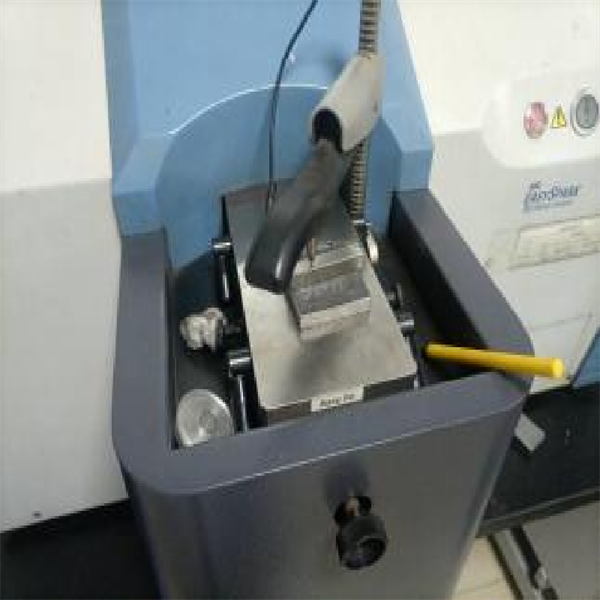
Hardness Testing
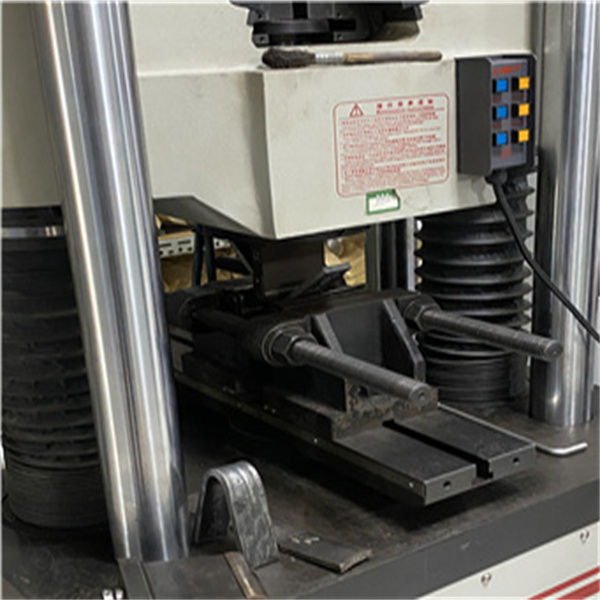
Bend Testing
Tensile testing of the pipe body—The tensile test should be carried out in accordance with ISO6892 or ASTM A370.Longitudinal samples should be used.Twice per test unit of pipe with the same cold-expansion ratio a.b.d.
flattening Test—One flattening test shall be made on specimens from each end of two tubes selected from each lot
CVN impact test—The Charpy test should be carried out in accordance with ASTM A370. Twice per test unit of not more than 100 lengths of pipe with the same cold-expansion ratio a.b.d.
Hardness Test—When suspected hard spots are detected by visual inspection, hardness tests shall be carried out in accordance with ISO 6506, ISO 6507, ISO 6508 or ASTM A 370 using portable hardness test equipment and methods complying with ASTM A 956, ASTM A 1038 or ASTM E 110 respectively depending on the method Used.
Hydro-static Test—Each tube shall be subjected to the hydro-static pressure test
Bending Test— a sufficient length of pipe shall stand being bent cold through 90° around a cylindrical mandrel.
100% X-ray test for the weld seam
The ultrasonic testing
The eddy current examination
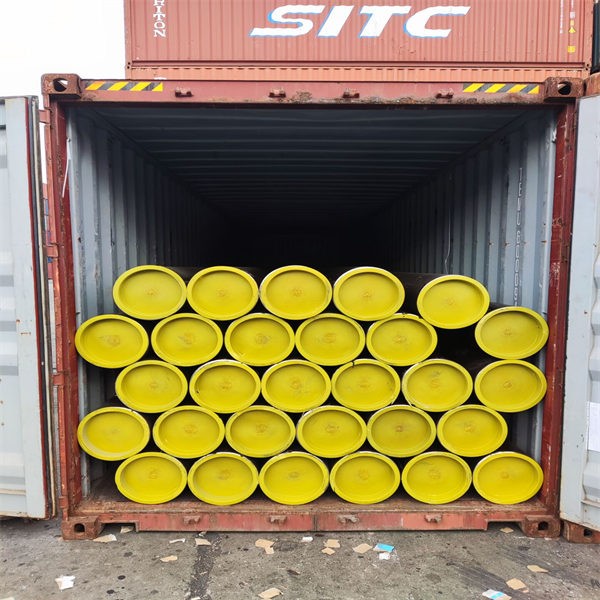
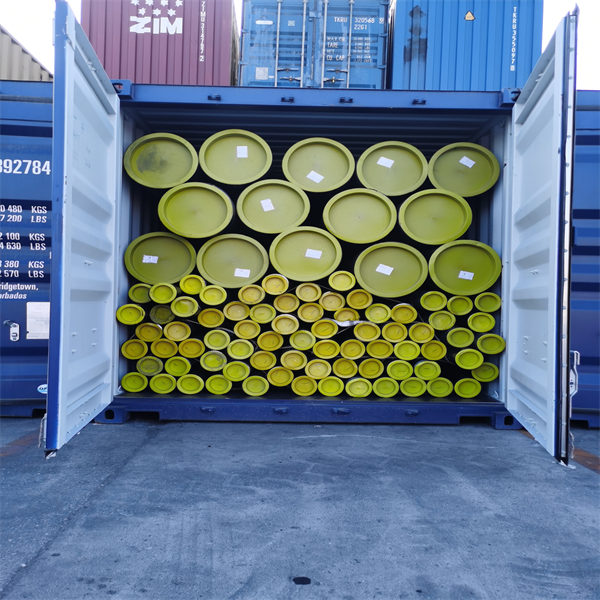
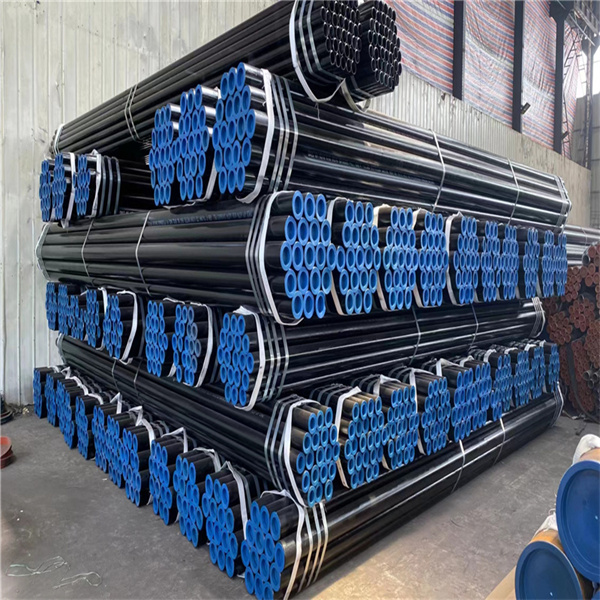
Bare pipe or Black / Varnish coating ( according to customer's requirements);
6" and below in bundles with two cotton slings;
Both ends with end protectors;
Plain end, bevel end(2" and above with bevel ends, degree: 30~35°), threaded and coupling;
Marking.
Size |
Tolerance (with respect to specified outside diameter) |
<2 3/8 |
+ 0.016 in., - 0.031 in. (+ 0.41 mm, - 0.79 mm) |
> 2 3/8 and ≤4 1/2, continuous welded |
±1.00% |
> 2 3/8 and < 20 |
±0.75% |
> 20. seamless |
± 1.00% |
>20 and <36, welded |
+ 0.75%.-0.25% |
> 36, welded |
+ 1/4 in.. - 1/8 in. (+ 6.35 mm, -3.20 mm) |
ln the case of pipe hydro-statically tested to pressures in excess of standard test pressures, other tolerances may be agreed upon between the manufacturer and the purchaser.
Out-of-Roundness | |||||
Size | Minus Tolerance | Plus Tolerance | End-to-End Tolerance | Diameter,Axis Tolerance (Percent of Specified OD) | Maximum Differential Between Minimum and Maximum Diameters (Applies Only to Pipe With D/t≤75) |
≤10 3/4 l&V4 | 1/64(0.40mm) | 1/16(1.59mm) | — | — | |
>10 3/4 and ≤20 | 1/32 (0.79 mm) | 3/32 (2.38 mm) | — | — | — |
> 20 and ≤ 42 | 1/32 (0.79 mm) | 3/32 (2.38 mm) | b | ± 1% | <0.500 in. (12,7 mm) |
>42 | 1/32 (0.79 mm) | 3/32 (2.38 mm) | b | ± 1% | £ Q625 in. (15.9 mm) |
Out-of-roundness tolerances apply to maximum and minimum diameters as measured with a bar gauge, caliper, or device measuring actual maximum and minimum diameters.
The average diameter (as measured with a diameter tape) of one end of pipe shall not differ by more than 3/32 in. (2.38 mm) from that of the other end.
Size | Type of Pipe | Tolerance1 (Percent of Specified Wall Thickness} | |
Grade B or Lower | Grade X42 or Higher | ||
<2 7/8 | All | +20.- 12.5 | + 15.0.-12.5 |
>2 7/8and<20 | All | + 15,0,-12.5 | + 15-I2.5 |
>20 | Welded | + 17.5.-12.5 | + 19.5.-8.0 |
>20 | Seamless | + 15.0.-12.5 | + 17.5.-10,0 |
Where negative tolerances smaller than those listed are specified by the purchaser, the positive tolerance shall be increased to the applicable total tolerance range in percent less the wall thickness negative tolerance.
Quantity |
Tolerance (percent) |
Single lengths, special plain-end pipe or A25 pipeSingle lengths, other pipeCarloads.GradeA25,40,000lb(18 144kg)or moreCarloads, other than Grade A25,40.0001b (18 144 kg) or moreCarloads, all grades less than 40000 lb (18 144 kg)
Order items. Grade A25. 40.000 lb (18 144 kg) or more Order items, other than Grade A25,40,000 lb (18 144 kg) or more Order items, all grades, less than 40.000 lb (18 144 kg) |
+ 10.-5.0 + 10,- 35 -2.5 -1.75 -15 -3.5 -1.75 -3.5 |
Notes:
1.Weight tolerances apply to the calculated weights for threaded-and-coupled pipe and to the tabulated or calculated weights for plain-end pipe. Where negative wall thickness tolerances smaller than those listed in above table are specified by the purchaser, the plus weight tolerance for single lengths shall be increased to 22.5 percent less the wail thickness negative tolerance.
2.For carloads composed of pipe from more than one order item, the carload tolerances are to be applied on an individual order item basis.
3. The tolerance for order items apply to the overall quantity of pipe shipped for the order item.