The API 5L standard names tubes based on their minimum yield strength. Therefore, X52 (L360) has a minimum yield strength of 52,200 psi (360 MPa).
X52=L360, are two ways of expressing the same pipe grade in API 5L standard.
X52 is an intermediate grade in API 5L, combining high strength with economy. Widely used in oil and gas transportation, construction projects, submarine pipelines, etc.
Botop Steel is a professional manufacturer of thick-walled large-diameter double-sided submerged arc LSAW steel pipe located in China.
1. Location: Cangzhou City, Hebei Province, China;
2. Total Investment: 500 million RMB;
3. Factory area: 60,000 square meters;
4. Annual production capacity: 200,000 tons of JCOE LSAW steel pipes;
5. Equipment: Advanced production and testing equipment;
6. Specialization: LSAW steel pipe production;
7. Certification: API 5L certified.
API 5L X52 Classification
Depending on the PSL level and delivery condition, X52 can be categorized as follows:
PSL1: X52;
PSL2: X52N or L360N; X52Q or L360Q; X52M or L360M.
In PSL2, the suffix letter refers to the type of heat treatment the material is to be subjected to before final delivery. You can see the delivery conditions below for more details.
Delivery Conditions
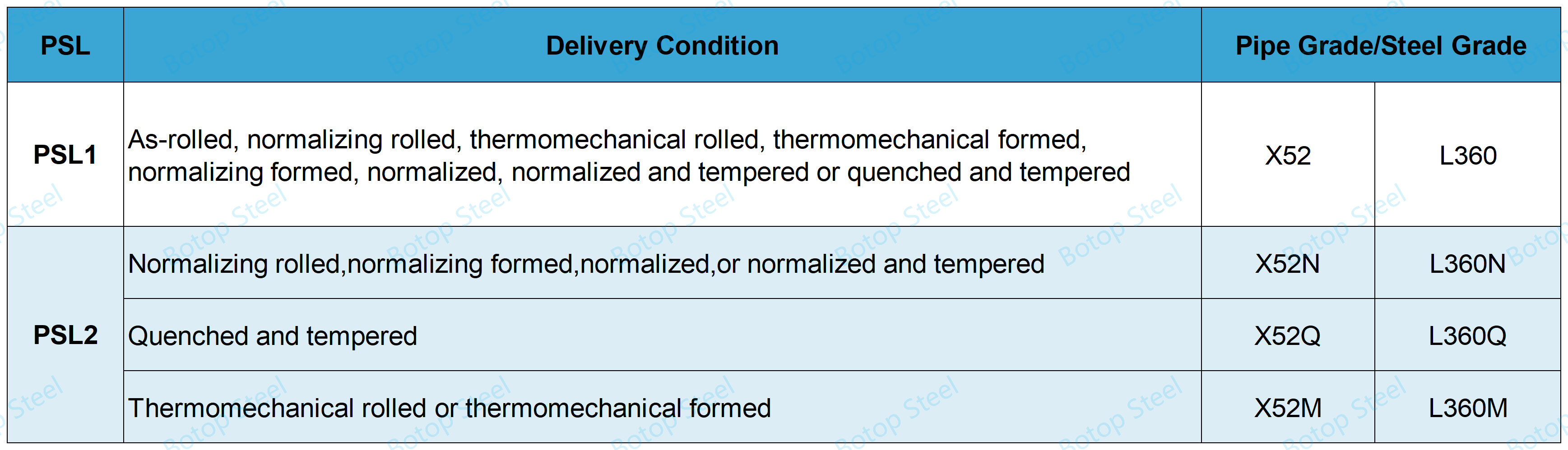
Starting Material
Ingots, blooms, billets, coils, or plates.
For PSL 2 pipe, the steel shall be killed and made according to fine grain practice.
The coil or plate used for the manufacture of PSL 2 pipe shall not contain any repair welds.
API 5L X52 Manufacturing Process
X52 tubes can be produced using a variety of tube manufacturing processes to meet different engineering needs.

To find out more about the meaning of the acronym Manufacturing Process, click here.
SAWL is the optimum solution for large-diameter, thick-walled steel pipes.
The terms "SAWL" and "LSAW" both refer to Longitudinal Submerged Arc Welded, but are referred to differently in different regions. In contrast, the term "LSAW" is more widely used in the industry.
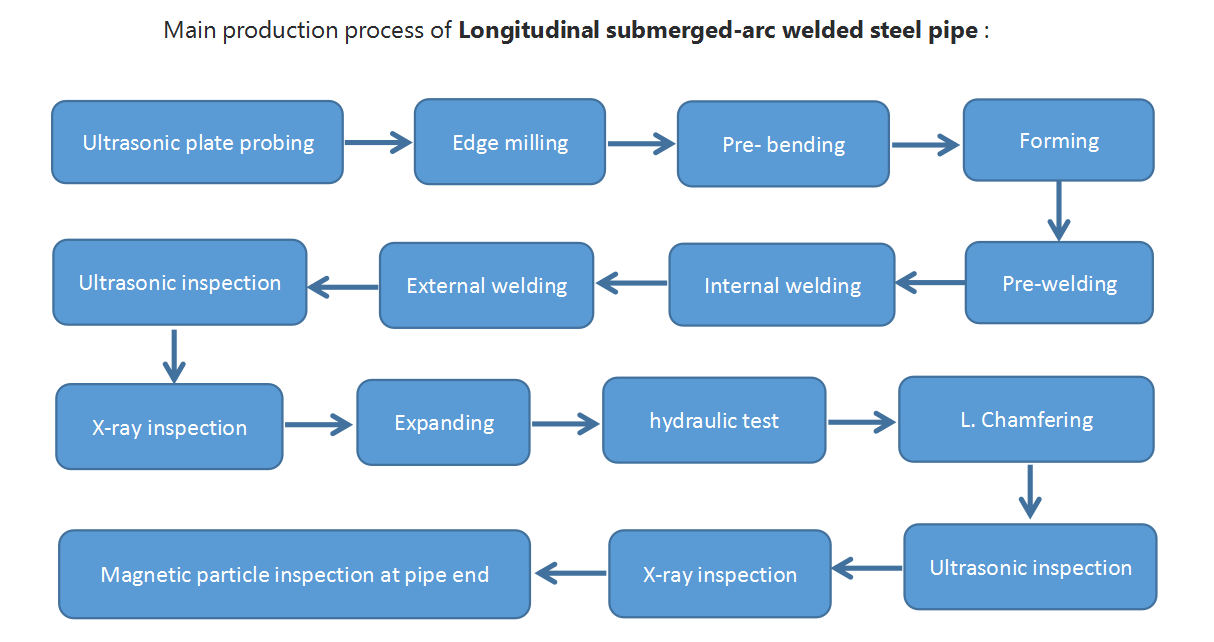
LSAW pipe may be double welded due to equipment limitations in the production of large-diameter pipe, and the welds should be approximately 180° apart.
Pipe End Types for API 5L X52
PSL1 Steel Pipe End: Belled end or Plain end;
PSL2 Steel Pipe End: Plain end;
For plain pipe ends the following requirements should be followed:
The end faces of t ≤ 3.2 mm (0.125 in) plain end pipe shall be square cut.
Plain-end tubes with t > 3.2 mm (0.125 in) shall be beveled for welding. The bevel angle should be 30-35° and the width of the root face of the bevel should be 0.8 - 2.4 mm (0.031 - 0.093 in).
API 5L X52 Chemical Composition
The chemical composition of PSL1 and PSL2 steel pipe t > 25.0 mm (0.984 in) shall be determined by agreement.
Chemical Composition for PSL 1 Pipe with t ≤ 25.0 mm (0.984 in.)
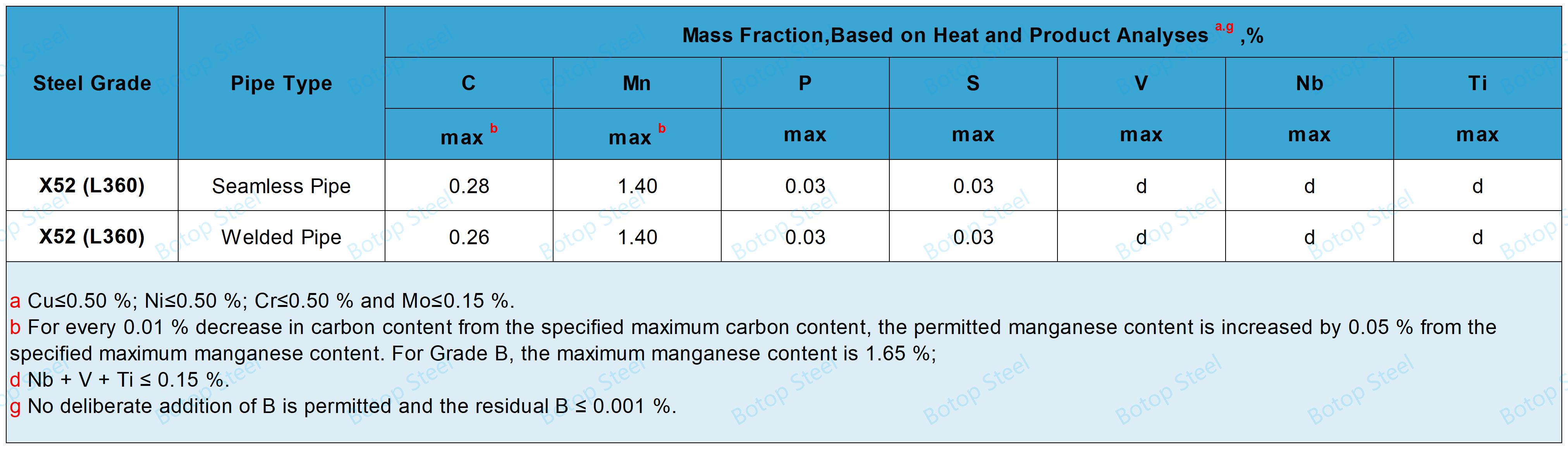
Chemical Composition for PSL 2 Pipe with t ≤ 25.0 mm (0.984 in.)
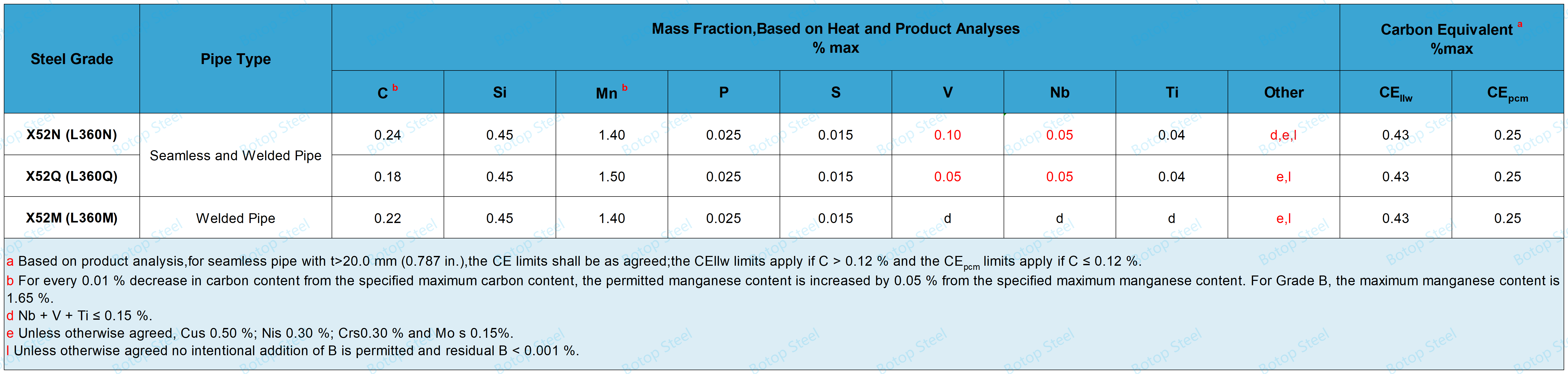
For PSL2 steel pipe products analyzed with a carbon content of ≤0.12%, the carbon equivalent CEpcm can be calculated using the following formula:
CEpcm = C + Si/30 + Mn/20 + Cu/20 + Ni/60 + Cr/20 + Mo/15 + V/15 + 5B
For PSL2 steel pipe products analyzed with a carbon content > 0.12%, the carbon equivalent CEllw can be calculated using the formula below:
CEllw = C + Mn/6 + (Cr + Mo + V)/5 + (Ni +Cu)/15
API 5L X52 Mechanical Properties
Tensile Properties
Tensile testing measures three key parameters: yield strength, tensile strength, and elongation.
PSL1 X52 Tensile Properties

PSL2 X52 Tensile Properties
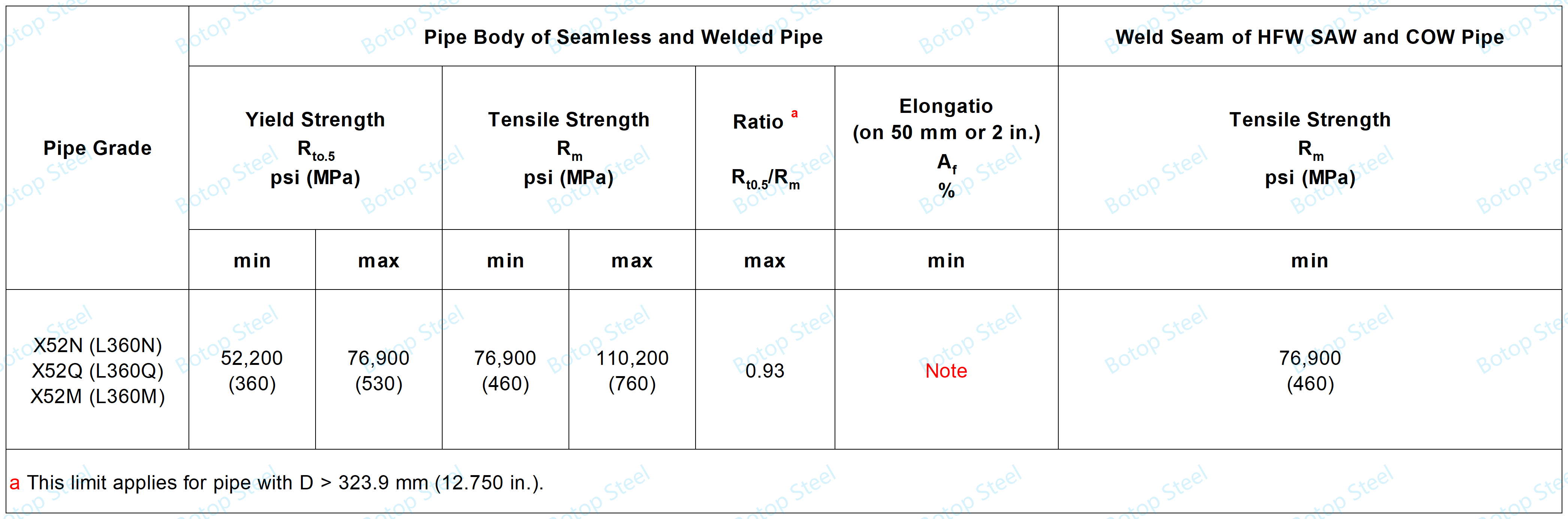
Note: The specified minimum elongation, Af shall be as determined using the following equation:
Af = C × (Axc0.2/U0.9)
C is 1940 for calculations using SI units and 625,000 for calculations using USC units;
Axc is the applicable tensile test piece cross-sectional area, expressed in square millimeters (square inches), as follows:
1) for circular cross-section test pieces, 130 mm2 (0.20 in.2) for 12.7 mm (0.500 in.) and 8.9 mm (0.350 in.) diameter test pieces; 65 mm2(0.10 in.2) for 6.4 mm (0.250 in.) diameter test pieces;
2) for full-section test pieces, the lesser of a) 485 mm2 (0.75 in.2) and b) the cross-sectional area of the test piece, T derived using the specified outside diameter and the specified wall thickness of the pipe, rounded to the nearest 10 mm2 (0.01 in.2);
3) for strip test pieces, the lesser of a) 485 mm2 (0.75 in.2) and b) the cross-sectional area of the test piece, derived using the specified width of the test piece and the specified wall thickness of the pipe, rounded to the nearest 10 mm2 (0.01 in.2);
U is the specified minimum tensile strength, expressed in megapascals (pounds per square inch).
Other Mechanical Experiments
The following test program applies to SAW pipe types. For other pipe types, see Tables 17 and 18 of API 5L.
Weld guide bending test;
Cold-formed welded pipe hardness test;
Macro inspection of welded seam;
and only for PSL2 steel pipe: CVN impact test and DWT test.
Hydrostatic Test
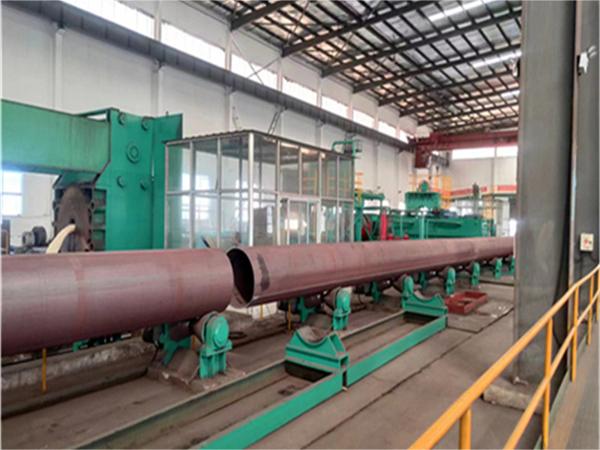
Test Time
All sizes of seamless and welded steel tubes with D ≤ 457 mm (18 in.): test time ≥ 5s;
Welded steel pipe D > 457 mm (18 in.): test time ≥ 10s.
Experimental Frequency
Each steel pipe.
Test pressures
The hydrostatic test pressure P of a plain-end steel pipe can be calculated by using the formula.
P = 2St/D
S is the hoop stress. the value is equal to the specified minimum yield strength of the steel pipe x a percentage, in MPa (psi);
t is the specified wall thickness, expressed in millimeters (inches);
D is the specified outside diameter, expressed in millimeters (inches).
Nondestructive Inspection
For SAW tubes, two methods, UT (ultrasonic testing) or RT (radiographic testing), are usually used.
ET (electromagnetic testing) is not applicable to SAW tubes.
Welded seams on welded pipes of grades ≥ L210/A and diameters ≥ 60.3 mm (2.375 in) shall be nondestructively inspected for full thickness and length (100 %) as specified.
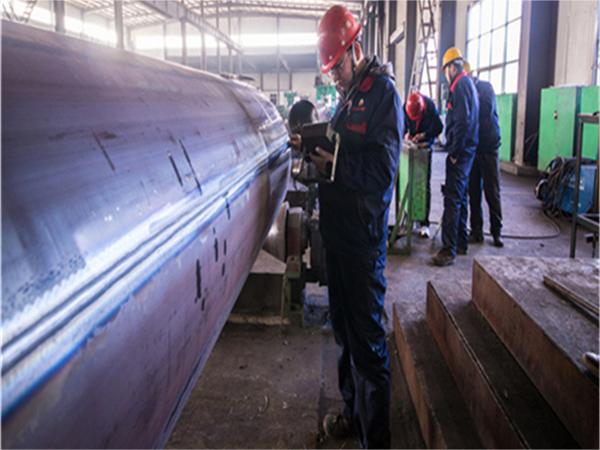
UT non-destructive examination
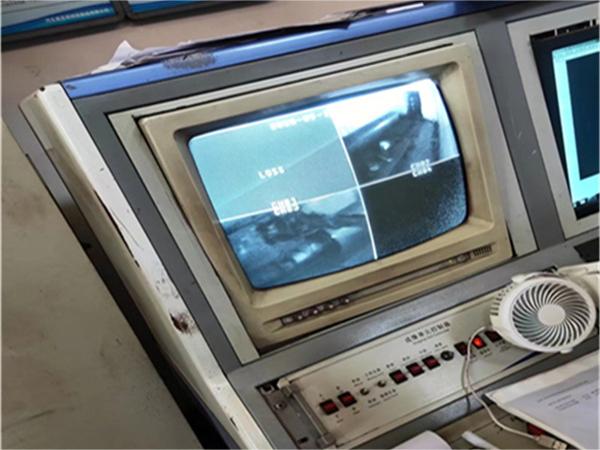
RT non-destructive examination
Cold Sizing and Cold Expansion
Cold sizing and cold expansion are two common processing techniques used in the production of LSAW tubes to ensure that the tubes achieve precise dimensions and mechanical properties. Both processes are cold working processes, where the shape and size of the tube are adjusted at room temperature.
The sizing ratio of cold expansion tubes shall not be less than 0.003 and shall not be greater than 0.015.
The sizing rate of cold-sized steel pipe shall not be greater than 0.015, except in the following cases:
a) The pipe is subsequently normalized or quenched and tempered;
b) The entire cold-sized steel tube is subsequently stress-relieved.
Specify Outside Diameter and Wall Thickness
Standardized values for specified outside diameters and specified wall thicknesses of steel pipe are given in ISO 4200 and ASME B36.10M.
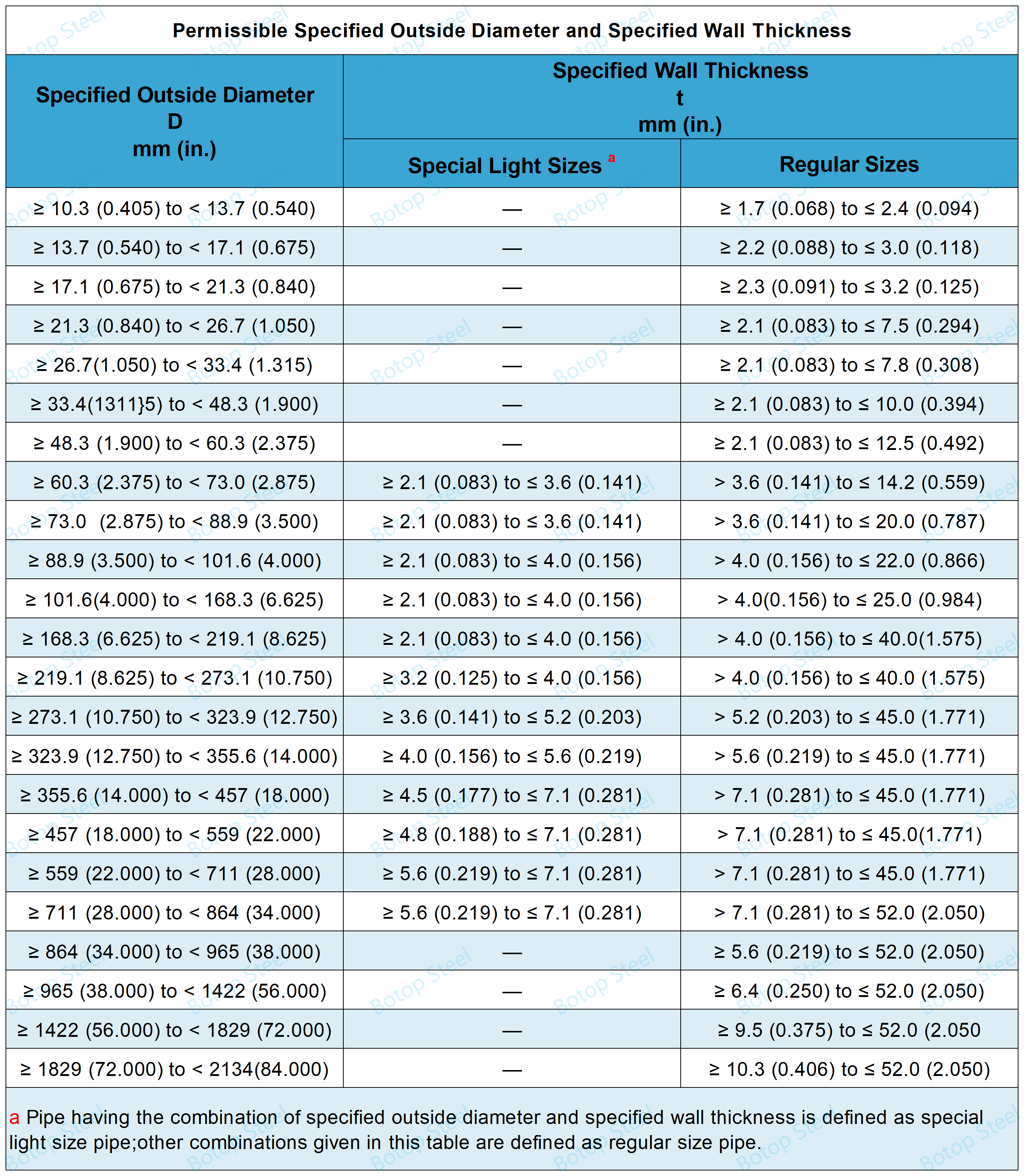
Dimensional Tolerances
Please click on the blue font on the right to view the dimensional tolerances, the requirements are listed in API 5L Grade B for details.
API 5L X52 Applications
API 5L X52 steel pipe is widely used in several critical applications due to its excellent mechanical properties and ability to adapt to complex environments.
Oil and gas transportation: This is one of the most common applications for API 5L X52. Mainly used for long-distance oil and gas transportation pipelines, especially when there is a high internal pressure.
Construction and infrastructure: Can be used to construct support structures for bridges and buildings. It can also be used in the manufacture of braces or other load-bearing structures, especially where long spans or high load-bearing capacities are required.
Subsea pipelines: Subsea pipeline projects have a particular need for corrosion-resistant and high-strength pipes, and API 5L X52 excels in this regard. It resists seawater and maintains the integrity and functionality of the pipeline, making it ideal for connecting to offshore oil and gas resources.
Our Supply Range
Standard: API 5L;
PSL1: X52 or L360;
PSL2: X52N, X52Q, X52M or L360N, L360Q, L360M;
Pipe Type: Welded Carbon Steel Pipe;
Manufacturing Process: LSAW, SAWL or DSAW;
Outer Diameter: 350 – 1500;
Wall Thickness: 8 - 80mm;
Length: Approximate lengths or random length;
Pipe Schedules: SCH10, SCH20, SCH30, SCH40, SCH60, SCH80, SCH100, SCH120, SCH140 and SCH160.
Identification: STD, XS, XXS;
Coating: Paint, varnish, 3LPE, FBE, 3LPP, HDPE, galvanized, epoxy zinc-rich, cement weighted, etc.
Packing: Waterproof cloth, wooden case, steel belt or steel wire bundling, plastic or iron pipe end protector, etc. Customized.
Matching Products: Bends, flanges, pipe fittings, and other matching products are available.