ASTM A513 steel is a carbon and alloy steel pipe and tube made from hot-rolled or cold-rolled steel as raw material by resistance welding (ERW) process, which is widely used in all kinds of mechanical structures.
Type 5 within the ASTM A513 standard refers to the Drawn Over Mandrel (DOM) tubing.
DOM tubing is produced by first forming a welded tube and then cold drawing it through dies and over mandrels to finish to a closer dimensional tolerance and smoother surface finish compared to other types of welded tubing.
Execution standard: ASTM A513
Material: Hot-rolled or Cold-rolled Steel
Type: Type1 (1a or 1b), Type2, Type3, Type4, Type5, Type6.
Grade: MT 1010, MT 1015,1006, 1008, 1009 etc.
Heat treatment: NA, SRA, N.
Size and wall thickness
Hollow section shape: Round, square, or other shapes
Length
Total Quantity

ASTM A513 Types are differentiated on the basis of different conditions or processes of the steel pipe.
ASTM A513 round tubing type 5 common grades are:
1008, 1009, 1010, 1015, 1020, 1021, 1025, 1026, 1030, 1035, 1040, 1340, 1524, 4130, 4140.
Round
Square or rectangular
Other shapes
such as streamlined, hexagonal, octagonal, round inside and hexagonal or octagonal outside, ribbed inside or out, triangular, rounded rectangular, and D shapes.

Hot-rolled or Cold-rolled Steel
The raw materials for the production of Hot-rolled or Cold-rolled Steel can be manufactured by any process.
Hot-Rolled Steel: In the production process, hot-rolled steel is first heated at high temperatures, allowing the steel to be rolled in a plastic state, which makes it easy to change the shape and size of the steel. At the end of the hot rolling process, the material is usually scaled and deformed.
Cold-Rolled Steel: Cold-rolled steel is rolled further after the material has cooled to achieve the desired size and shape. This process is usually done at room temperature and results in steel with better surface quality and more accurate dimensions.
Tubes shall be made by the electric-resistance-welded (ERW) process.
ERW pipe is the process of creating a weld by coiling a metallic material into a cylinder and applying resistance and pressure along its length.
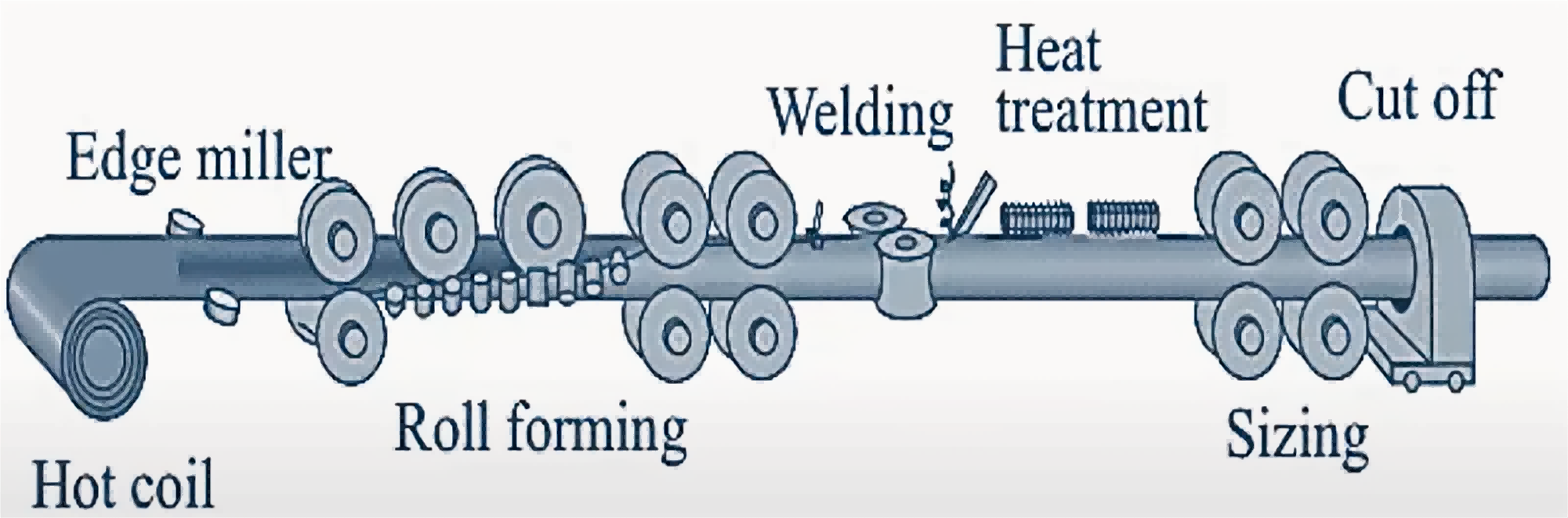
Steel shall conform to the chemical composition requirements specified in Table 1 or Table 2.

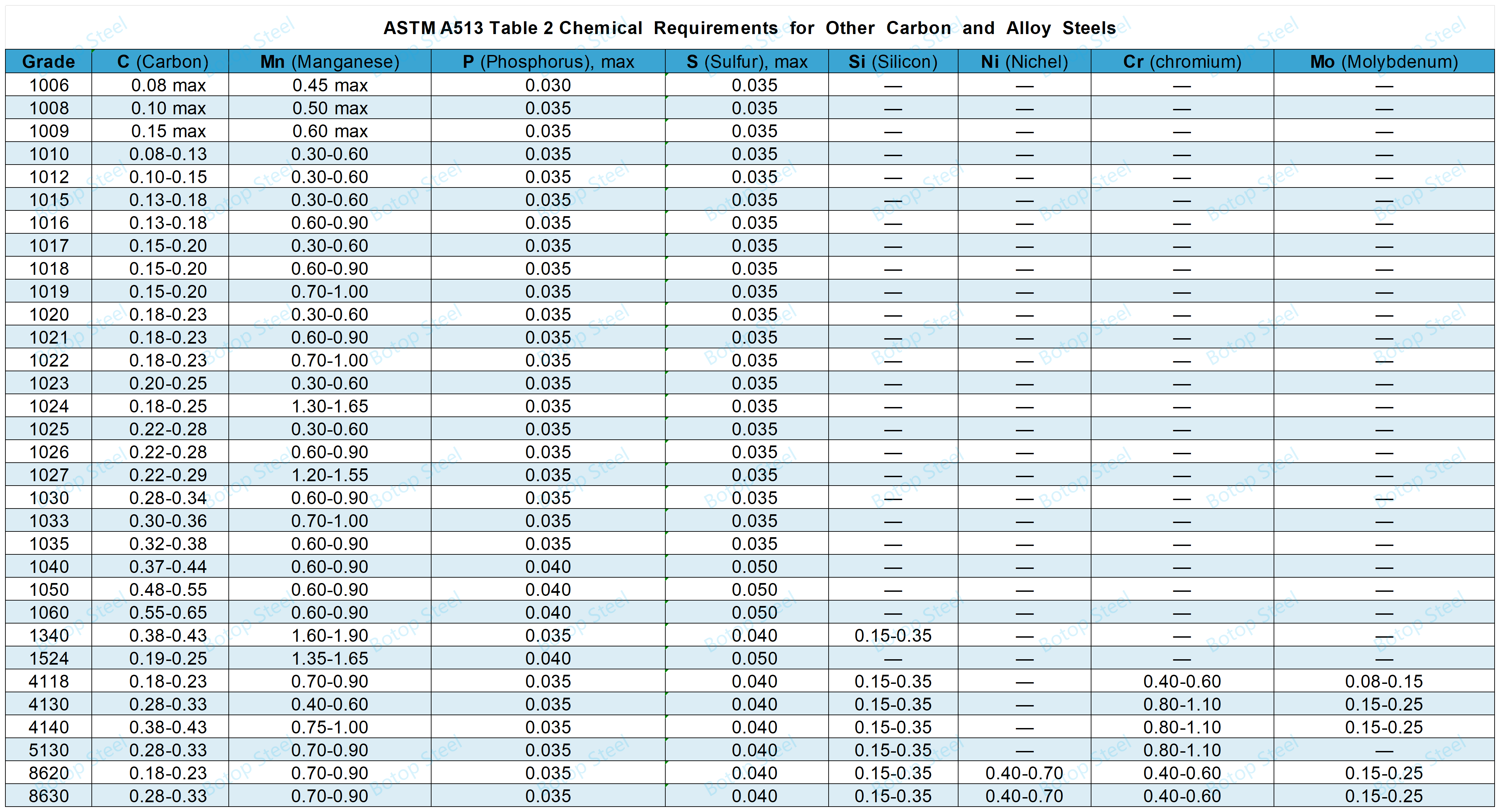
Grade | Yied Strength ksi[MPa],min |
Ultimate Strength ksi[MPa],min |
Elongation in 2 in.(50 mm), min, |
RB min |
RB max |
DOM Tubing | |||||
1008 | 50 [345] | 60 [415] | 5 | 73 | — |
1009 | 50 [345] | 60 [415] | 5 | 73 | — |
1010 | 50 [345] | 60 [415] | 5 | 73 | — |
1015 | 55 [380] | 65 [450] | 5 | 77 | — |
1020 | 60 [415] | 70 [480] | 5 | 80 | — |
1021 | 62 [425] | 72 [495] | 5 | 80 | — |
1025 | 65 [450] | 75 [515] | 5 | 82 | — |
1026 | 70 [480] | 80 [550] | 5 | 85 | — |
1030 | 75 [515] | 85 [585] | 5 | 87 | — |
1035 | 80 [550] | 90 [620] | 5 | 90 | — |
1040 | 80 [550] | 90 [620] | 5 | 90 | — |
1340 | 85 [585] | 95 [655] | 5 | 90 | — |
1524 | 80 [550] | 90 [620] | 5 | 90 | — |
4130 | 85 [585] | 95 [655] | 5 | 90 | — |
4140 | 100 [690] | 110[760] | 5 | 90 | — |
DOM Stress-Relieved Tubing | |||||
1008 | 45 [310] | 55 [380] | 12 | 68 | — |
1009 | 45 [310] | 55 [380] | 12 | 68 | — |
1010 | 45 [310] | 55 [380] | 12 | 68 | — |
1015 | 50 [345] | 60 [415] | 12 | 72 | — |
Note 1: These values are based on normal mill stress-relieving temperatures. For particular applications, properties may be adjusted by negotiation between the purchaser and producer.
Note 2: For longitudinal strip tests, the width of the gauge section shall be according to A370 Annex A2, Steel Tubular Products, and a deduction of 0.5 percentage points from the basic minimum elongation for each 1/32 in [0.8 mm] decrease in wall thickness under 5/16 in [7.9 mm] in wall thickness shall be permitted.
1% of all tubes in each lot and not less than 5 tubes.
Round tubes and tubes that form other shapes when they are round are applicable.
All tubing will be given a hydrostatic test.
Maintain the minimum hydro test pressure for not less than 5s.
The pressure is calculated as:
P=2St/D
P = minimum hydrostatic test pressure, psi or MPa,
S = allowable fiber stress of 14,000 psi or 96.5 MPa,
t = specified wall thickness, in. or mm,
D = specified outside diameter, in. or mm.
It is the intent of this test to reject tubes containing injurious defects.
Each tube shall be tested with a nondestructive electric test in accordance with Practice E213, Practice E273, Practice E309, or Practice E570.
Outer Diameter
Table 5 Diameter Tolerances for Types 3, 4, 5, and 6 (S.D.H.R., S.D.C.R., DOM, and S.S.I.D.) Round
Wall Thickness
Table 8 Wall Thickness Tolerances of Types 5 and 6 (DOM and S.S.I.D.) Round Tubing (Inch Units)
TABLE 9 Wall Thickness Tolerances of Types 5 and 6 (DOM and S.S.I.D.) Round Tubing (SI Units)
Length
Table 13 Cut-Length Tolerances for Lathe-Cut Round Tubing
Table 14 Length Tolerances for Punch-, Saw-, or Disc-Cut Round Tubing
Squareness
Table 16 Tolerances, Outside Dimensions Square and Rectangular Tubing
Mark the following information in an appropriate manner for each stick or bundle.
manufacturer name or brand, specified size, type, purchaser's order number, and this specification number.
Barcoding is acceptable as a supplementary identification method.
Tubing shall be coated with a film of oil before shipping to retard rust.
Should the order specify that tubing be shipped without rust retarding oil, the film of oils incidental to manufacture will remain on the surface.
It can effectively prevent the surface of the pipe from reacting with moisture and oxygen in the air, thus avoiding rust and corrosion.
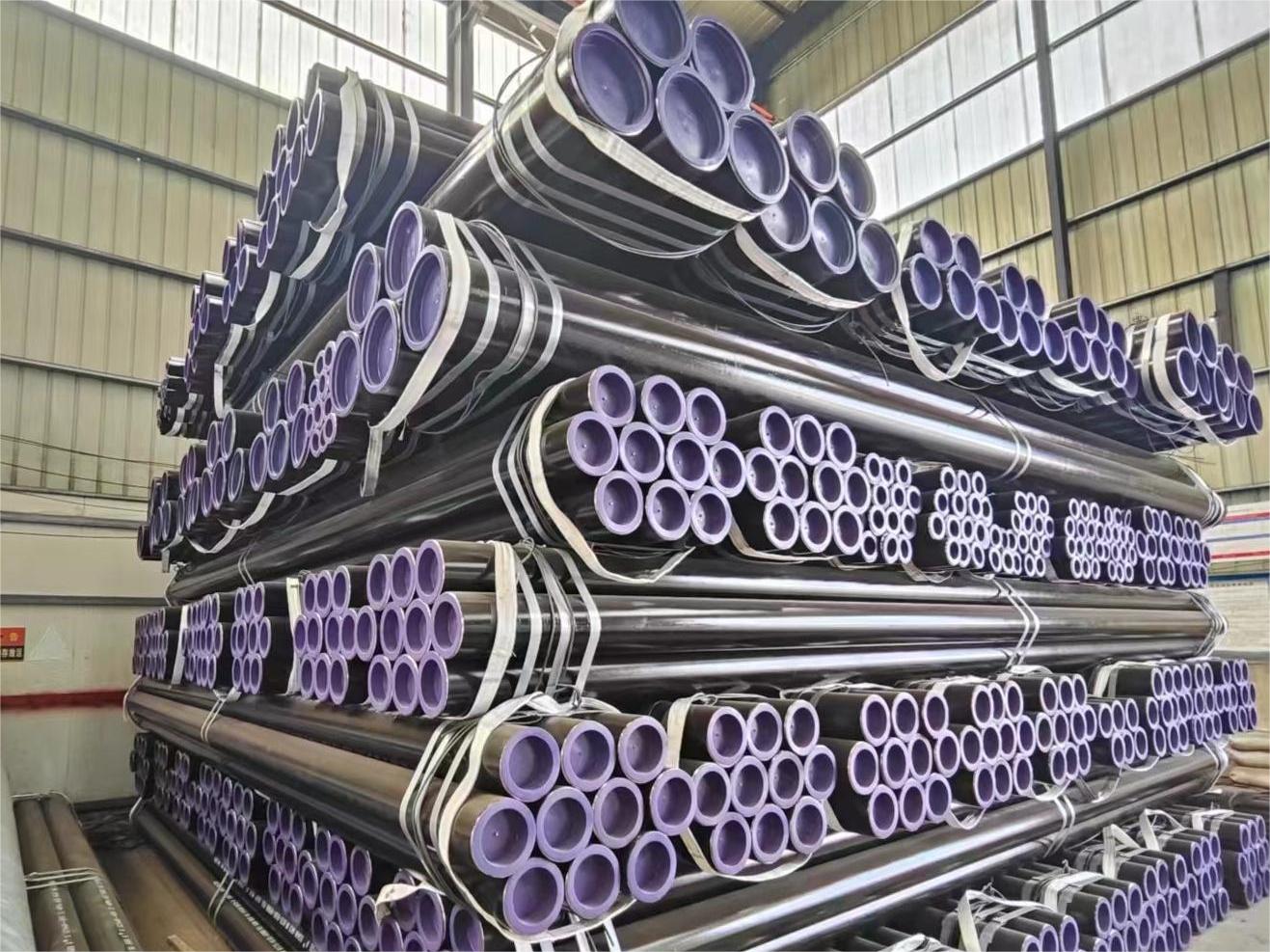
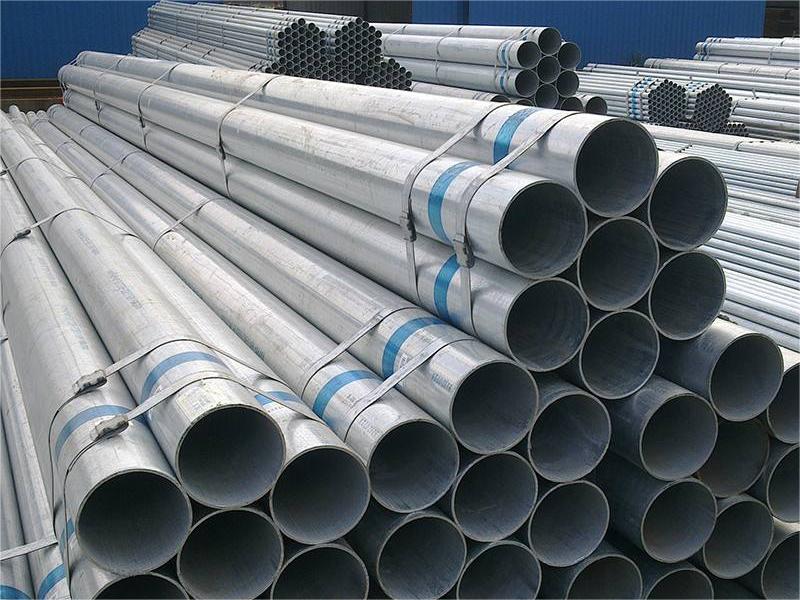
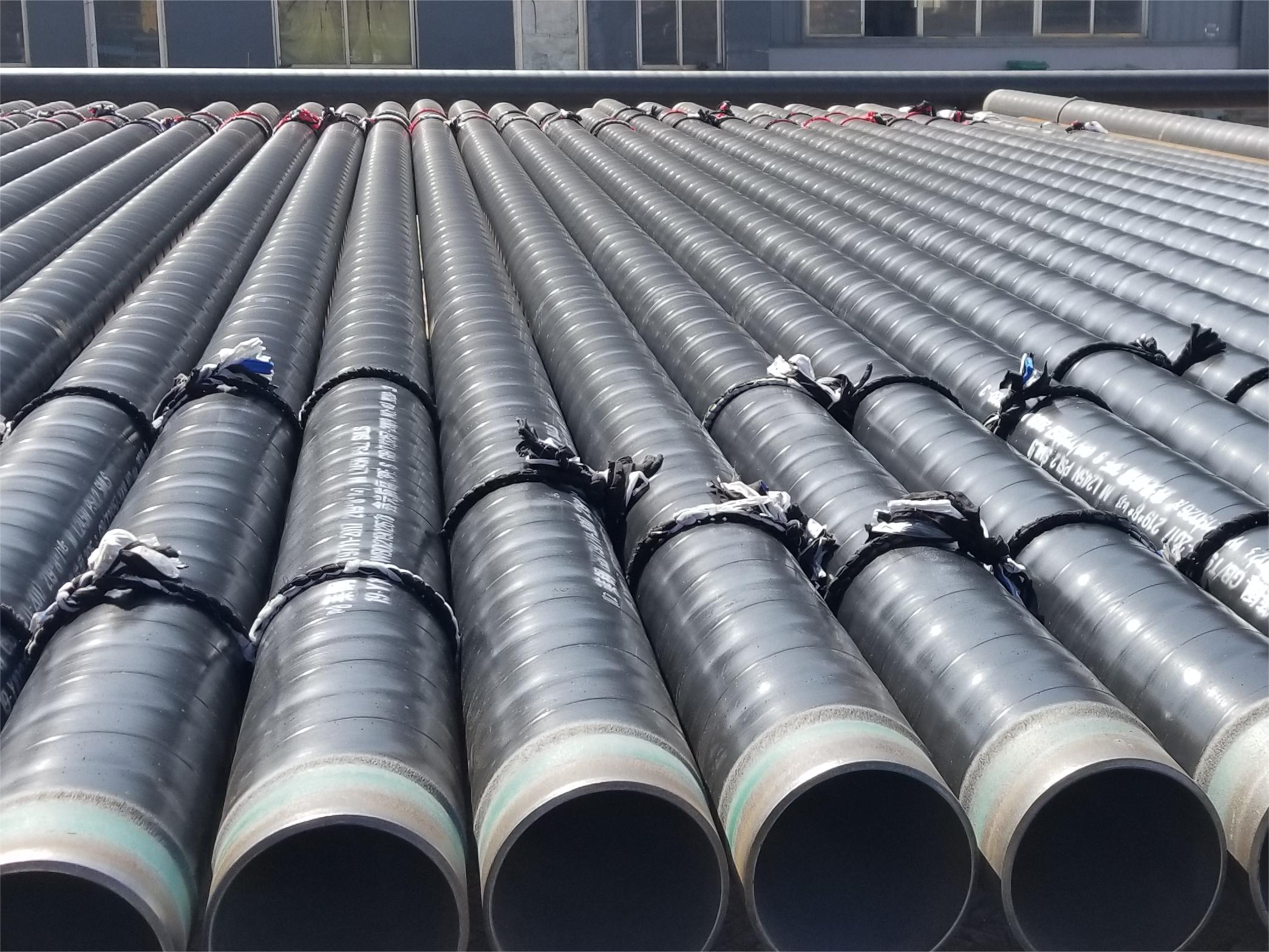
Indeed, while a basic lubricant or simple oil film can provide some degree of temporary protection, for applications requiring a higher level of protection, the appropriate corrosion protection treatment should be selected on a case-by-case basis.
For example, for buried pipelines, a 3PE (three-layer polyethylene) coating can be used to provide long-term corrosion protection; for water pipelines, an FBE (fusion-bonded epoxy powder) coating can be applied, while galvanized treatments can be an effective option in environments where protection against zinc corrosion is required.
With these specialized corrosion protection technologies, the service life of the pipe can be significantly extended and its functionality maintained.
High precision: Smaller dimensional tolerances than other welded tubes.
Surface quality: Smooth surfaces are ideal for applications requiring aesthetic appearance and minimal surface imperfections.
Strength and durability: The cold-drawing process enhances mechanical properties, making it suitable for high-stress applications.
Machinability: Easier to machine due to its uniform microstructure and consistent properties throughout the material.
Automotive industry: for the manufacture of key components such as drive shafts, bearing tubes, steering columns, and suspension systems.
Aerospace components: for the manufacture of bushings and non-critical structural components for aircraft.
Industrial machinery: Widely used in the manufacture of shafts, gears, etc., due to their ease of machining and durability.
Sporting goods: structural components such as high-performance bicycle frames and fitness equipment.
Energy sector: used in brackets or roller components for solar panels.
We are one of the leading welded carbon steel pipe and seamless steel pipe manufacturers and suppliers from China, with a wide range of high-quality steel pipe in stock, we are committed to providing you with a full range of steel pipe solutions.
For more product details, please feel free to contact us, we look forward to helping you find the best steel pipe options for your needs!