AWWA C213 steel water pipe is a FBE coating applied to the interior and exterior surfaces of steel pipe for use in underground or underwater steel water piping systems.
This coating provides protection against corrosion and ensures reliable operation of the pipeline system for extended periods of time in underground or submerged environments.
Pipe outer diameter ≥ 660mm [24in].Epoxy resin lining with access to the pipe for inspection and maintenance.
Steel pipe diameters <660mm [24in] may also be suitable, provided there is a suitable means of checking the integrity of the internal coating.
Fusion Bonded Epoxy (FBE) is a one-component dry powder thermosetting epoxy resin that, when activated by heat, creates a chemical reaction on the surface of steel pipe while maintaining its properties.
The epoxy powder shall consist of a one-component fusion bonded material consisting of an epoxy resin, curing agent, catalyst, filler, colorant, flow control agent, and UV inhibitor.

Materials shall comply with the requirements of the Safe Drinking Water Act.
When NSF compliance is required, materials in contact with potable water shall be certified to NSF/ANSI/CAN Standard 61.
In general, the maximum application temperature for coatings is approximately 65°C (150°F). Moreover, the service life of the coating is reduced by maintaining high temperatures for a long period of time.
When applied to preheated articles by electrostatic spraying, fluidized bed or air spraying and subsequently cured, the epoxy powder produces a uniform protective coating.
Specific operations are as follows:
Pipe Inspection and Pre-treatment
The surface shall be free of defects affecting the final product, such as burrs, gouges, and weld spatters, which can be removed by sanding.
and surfaces shall be free of mud, mill paint, wax, coal tar, asphalt, oil, grease, chlorides, and any other foreign matter or combustible contaminants that may ignite at fusion bonded epoxy application temperatures. Remove visible spots of oil and grease by wiping with a solvent that leaves no residue.
Surface Preparation
Use dry sandblasting to clean surface rust from steel pipe.
Blasting Environment Requirements: When the temperature of the steel pipe is 3°C (5℉) above the dew point temperature.
Surface Cleanliness: The surface of the descaled steel pipe shall be in accordance with SSPC-SP10/NACE No. 2.
Surface Roughness: Anchor grain depths in the range of 51-102 μm (2.0-4.0 mil )measured in accordance with ASTM D4417. This can be measured with an anchor pattern topper or an anchor pattern meter.
Surface roughness that is too deep or too shallow will affect the performance of the final FBE coating.
Note: Please note the time interval between the completion of the descaling and the coating process to avoid flash rusting.
Air Cleaning
Contaminant-free compressed air shall be used to blow the dust, grit, or other foreign matter from the prepared substrate of the pipe in a manner that does not affect the cleaned surface, other cleaned pipe, or pipe to be coated or lined.
Pipe Heating
Heat steel pipe using a heat source that must not contaminate the surface of the pipe, but must not exceed 274°C (525°F ).
Higher temperatures may alter the physical properties and toughness characteristics of the steel.
The surface temperature of the steel pipe can be measured using a thermometer pen or a calibrated optical thermometer.
If a blue color occurs, the pipe should be cooled to ambient temperature and re-blasted.
Coating Process
FBE powder is uniformly applied to the surface of the heated steel pipe by melting bed, electrostatic spraying, or air spraying.
Grooves, beveled, or root surfaces must not be FBE coated.
When rubber-gasketed joints or mechanical couplings are used, the epoxy shall extend to the ends of the pipe unless otherwise specified by the purchaser.
Cooling
Cooling can be done with air or water.
PQT: Purchase AWWA C213 Water Transmission Steel Pipe in small trial quantities before purchasing large quantities. Prequalification or testing is performed to ensure that a product or system meets specific quality and performance criteria.
This includes laboratory testing, performance evaluations, and other processes.
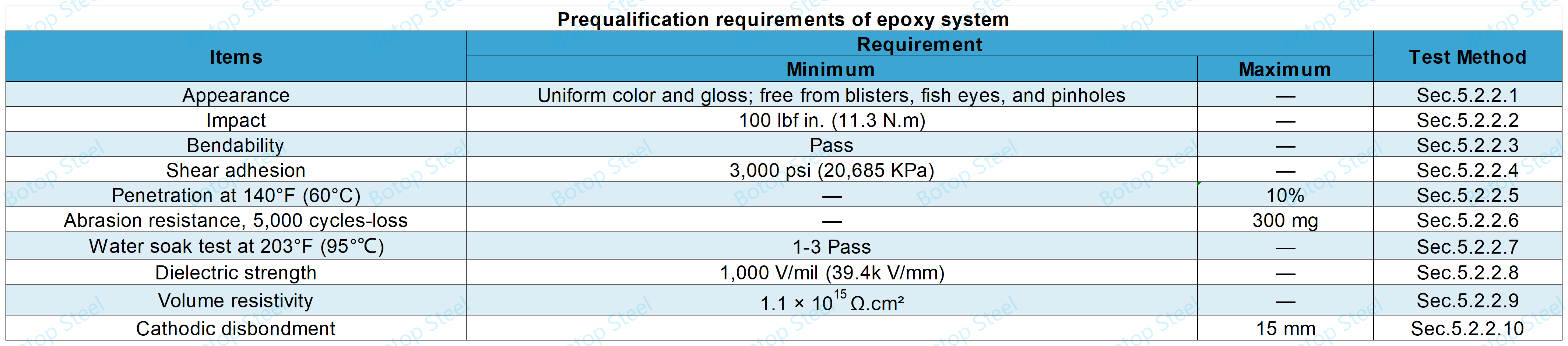
Appearances
The epoxy shall be generally smooth.
The epoxy shall have no blisters, cracks, bubbles, delamination, or other visible defects.
Cosmetic imperfections, such as sags, dimpling, scuffing, curtaining, over spray, and/or orange-peel, shall not be considered cause for rejection or repair.
Electrical inspection for continuity (low-voltage holiday test)
Coating continuity should be checked in accordance with NACE SPO490.
For linings with a thickness of 20 mils (508 um) or less, a low-voltage holiday detector set at a maximum of 75 V shall be used in accordance with NACE SPO188.
If the number of holidays exceeds the number below the coating will need to be removed and remanufactured.
Outside diameter (OD) <14in (360 mm), 1 holiday/meter (3 ft).
Outside diameter (OD) ≥ 14in (360 mm), 1 holiday/25 ft² (2.3 mm²).
Take the inspected holidays, repair them, and re-test them.
Adhesion
Adhesion of the cured epoxy to the surface of the pipe can be achieved by pushing a sharp blade through the epoxy onto the surface of the pipe and using a plowing motion in an attempt to remove the epoxy from the surface of the pipe.
The epoxy should be fully adhered to the pipe on the pipe firmly resist the plowing action and be free of brittle debris and meet an adhesion rating of 1-3.
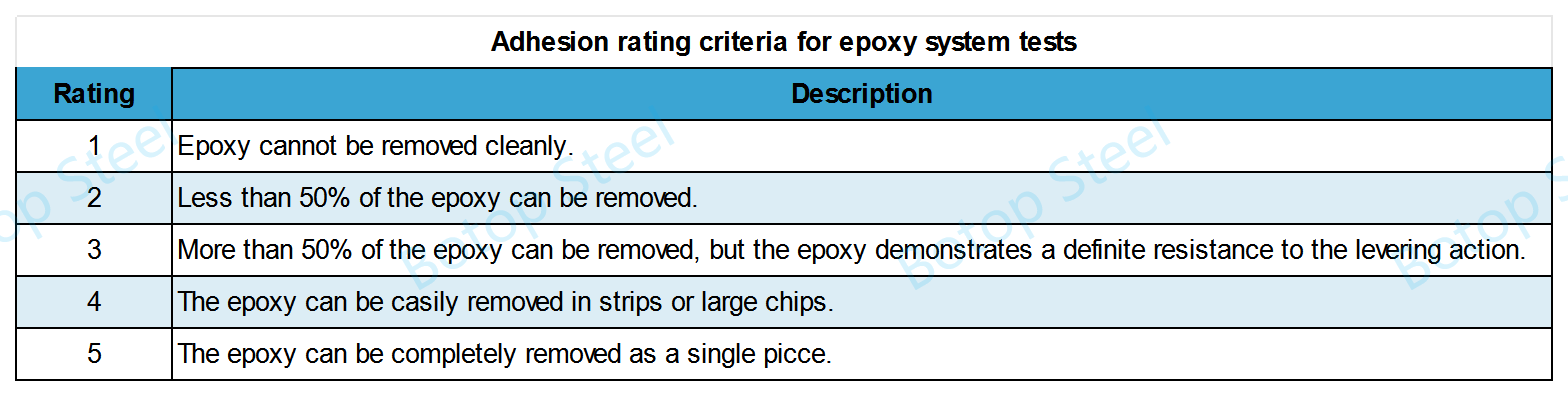
Thickness
The thickness of the cured coating film should not be less than 305um (12mil), including weld seams.
In the old version of AWWA C213, there was a limit of 406 um ( 16 mils ) maximum coating thickness, which has been removed in the latest version because of the difficulty in achieving this requirement during the actual generation process.
Additional Tests
Additional tests can be specified to determine the performance of the epoxy.
1. Cross-section porosity.
2. Interface porosity.
3. Thermal analysis (DSC).
4. Permanent strain (bendability).
5. Water soak.
6. Impact.
7. Cathodic disbondment test.
It shall be plainly marked with the name of the manufacturer, type of material, batch or lot number, date of manufacture, and storage conditions.
Mainly for water supply pipes
External coatings are typically used to protect pipes from environmental corrosion, while internal coatings are used to prevent water contamination, reduce frictional resistance, and extend pipe life. These coatings help ensure the reliability and durability of piping systems, comply with sanitary standards, and reduce the need for maintenance.
ANSI/AWWA C203: Coal-Tar Protective Coatings and Linings for Steel Water Pipe.
ANSI/AWWA C209: Tape Coatings for Steel Water Pipe and Fittings.
ANSI/AWWA C210: Liquid-Epoxy Coatings and Linings for Steel Water Pipe and Fittings.
Botop Steel is a high-quality Welded Carbon Steel Pipe manufacturer and supplier from China, also a seamless steel pipe stockist.
Botop Steel has a strong commitment to quality and implements rigorous controls and testing to ensure product reliability. Its experienced team provides personalized solutions and expert support, with a focus on customer satisfaction. We look forward to working with you.