DIN 30670-1 is a three-layer extrusion process that produces a polyethylene (3LPE) coating on the surface of longitudinally or spirally welded and seamless steel pipes to protect them from corrosion.
It is mainly used in buried or submerged piping systems for the transportation of liquids or gases.
Note: DIN 30670 has been divided into two parts in the latest 2024 edition depending on the production process, namely DIN 30670-1 covers hose and wound extruded polyethylene coatings, and DIN 30670-2 covers sintered and flame sprayed types.
They are divided into two types according to the design temperature, which are type N and type S.
Type | Design temperature (°C) |
N | -20 to + 60 |
S | -40 to + 80 |
and ISO 21809-1 corresponds to class A and class B, respectively.
1st layer Epoxy resin layer, epoxy resin powder must be used.
2nd Adhesive layer, which can be powder or extruded coated.
3rd layer Polyethylene layer, tube extrusion process, or winding extrusion process.
Tube Extrusion:
In this process, the polyethylene material is extruded directly into a continuous tubular form, which is then socketed onto the steel pipe.
This method is usually used for smaller diameter pipes and ensures uniformity and continuity of the coating.
Winding extrusion:
In this process, the polyethylene is extruded in the form of a strip and then wound onto the surface of the steel pipe.
This method is suitable for large-diameter or non-standard-sized pipes and allows for more flexible coatings on complex or large-sized pipes.
Depending on the specific needs of the project, an additional layer of mechanical protection can be added to the 3LPE.
Commonly used materials include concrete (refer to ISO 21809-5), glass fiber-reinforced plastic, or cement mortar (refer to DN N 30340-1).
To ensure good shear strength, it is necessary to rough or pressurize the surface of the polyethylene.
Such treatment helps to increase the adhesion between the additional protective layer and the polyethylene coating.
Epoxy Resin Layer Thickness
Minimum 80um.
Adhesive Layer Thickness
Minimum 150um.
Total Coating Thickness
Depending on the nominal diameter of the steel pipe, the thickness of the corrosion protection layer will be different.
For the total thickness of the 3LPE layer, DIN 30670-1 divides three classes to cope with different construction requirements. n,v, and s.

Grade n: For normal conditions, the thickness of grade n is usually sufficient.
For coatings of polyethylene, a thickness of 1 mm is used primarily for corrosion protection, while the remaining thickness is used to enhance the mechanical load-bearing capacity of the protective layer.
Grade v: If the mechanical load increases (transportation, storage, laying, specific quality, increased requirements), the minimum coating thickness must be increased by 0.7 mm, i.e. v = n + 0.7 mm.
Grade s: Special coating thicknesses higher than v can also be agreed upon to meet the needs of a specific project, and such customized coating thicknesses are labeled as Grade s.
150mm ± 20mm, the bevel angle for coating thickness should be no more than 30°.
The epoxy and adhesive layers shall be removed at least 80 mm from the pipe end. The epoxy layer shall be left protruding from the polyethylene-coated pipe end by not less than 10 mm.
To determine the length, measure from the root surface of the pipe to the beginning of the diagonal cut end of the corrosion protection layer.
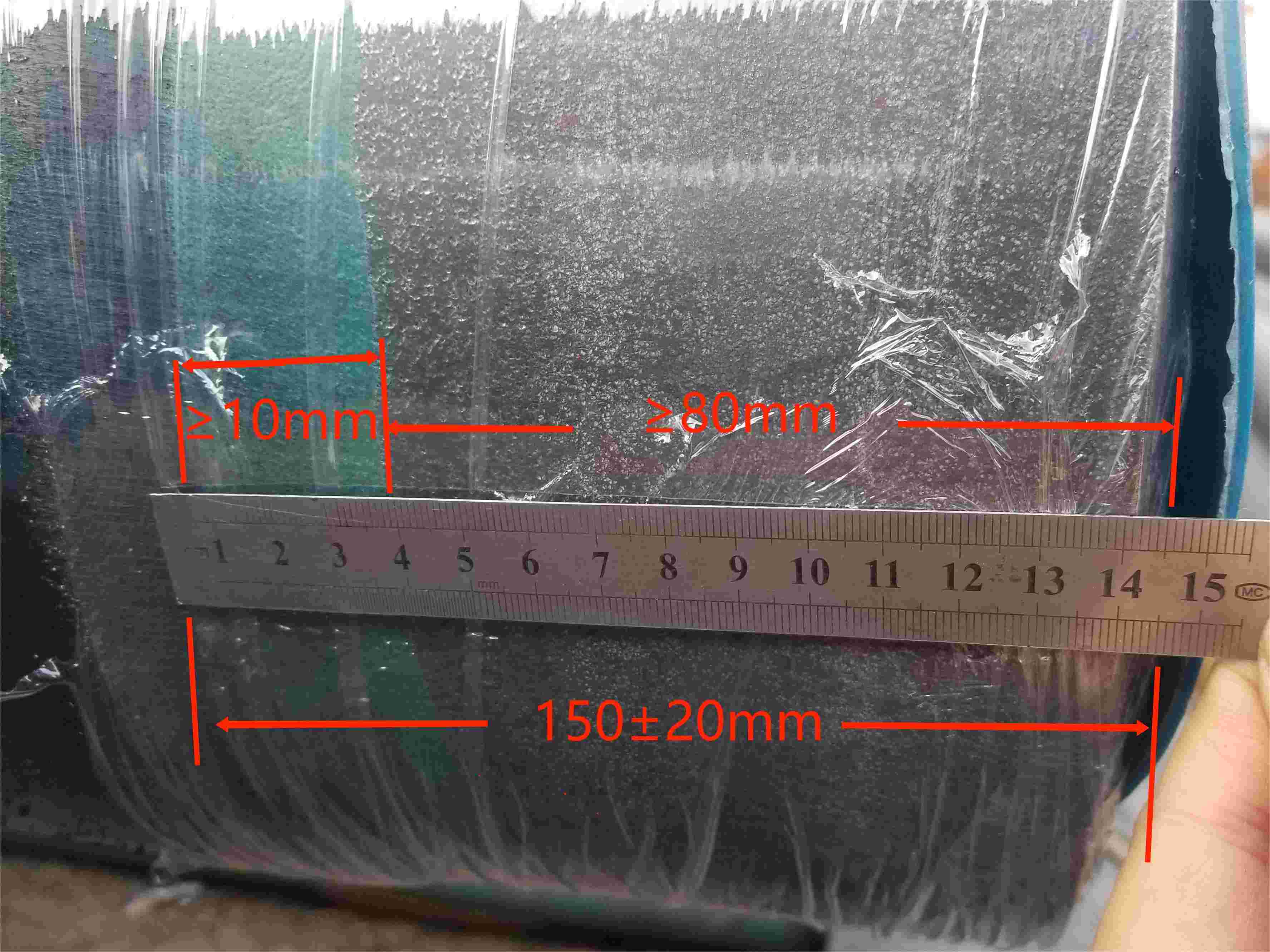
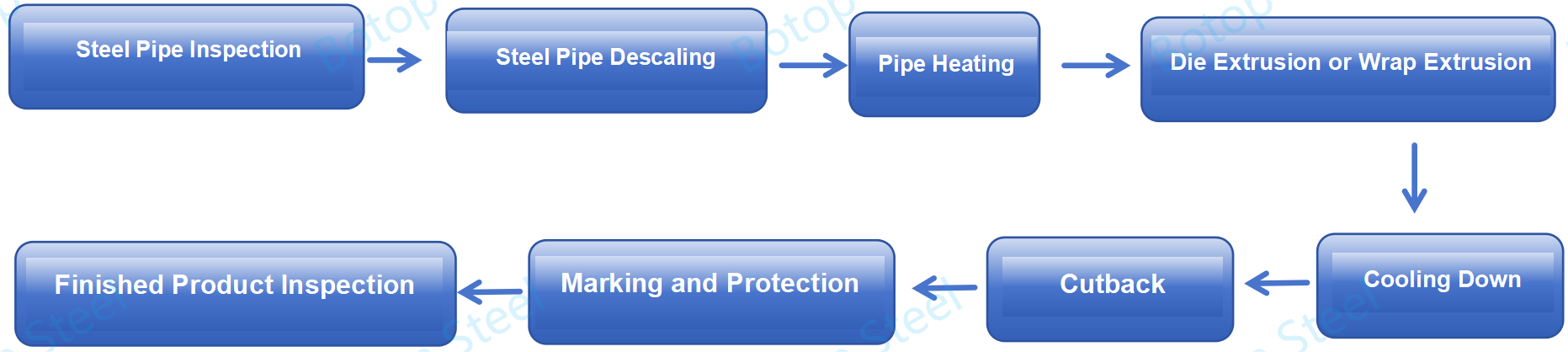
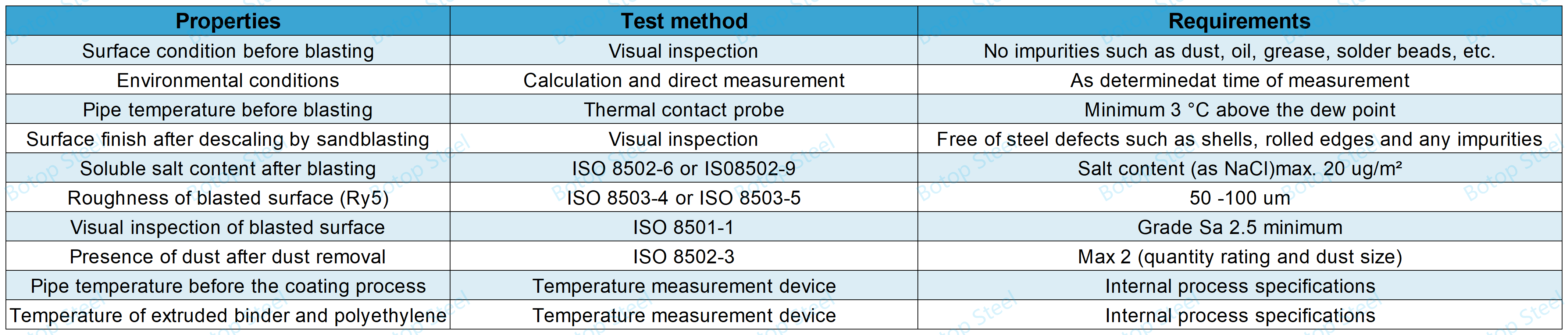
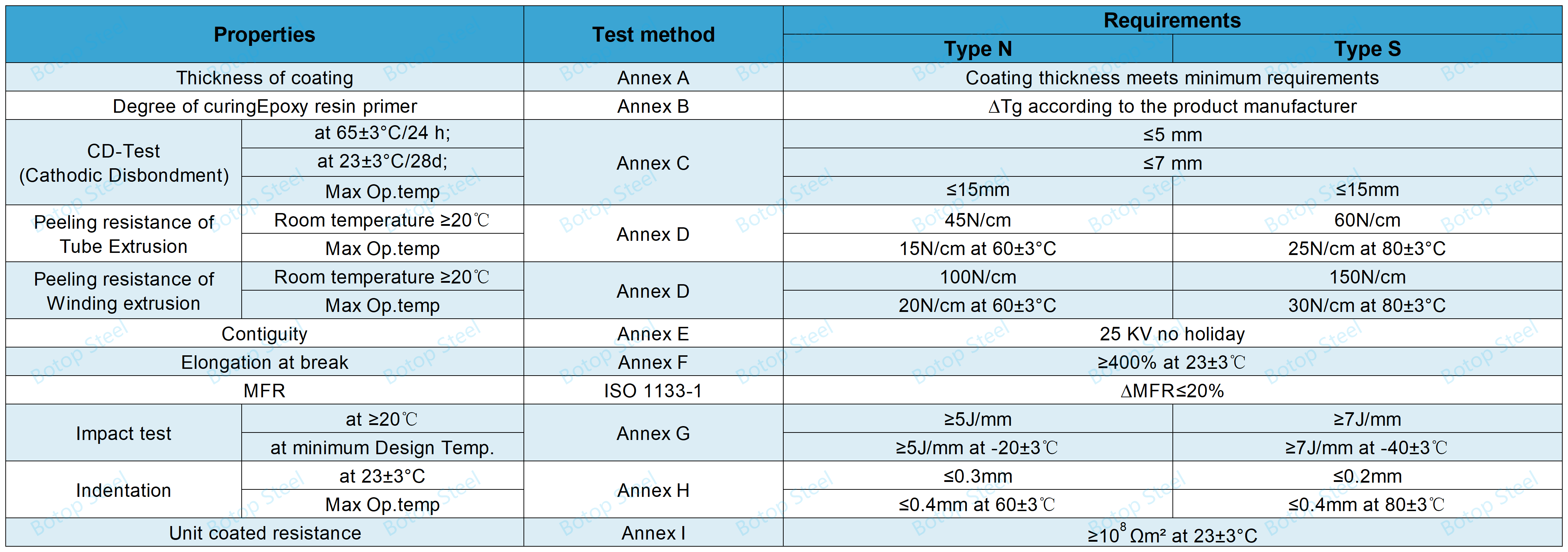
General Defects
Minor imperfections and damage to the surface of the steel not reached.
Holes in the top layer of PE;
Smaller areas with incomplete coverage;
Inclusions and air bubbles in the top layer;
Adhesion of foreign substances;
Surface abrasion;
Small dents in the coating.
These minor injuries are permitted to be repaired and there is no limit to the area that can be repaired.
Severe Defects
Coating damage is straight to the surface of the steel pipe.
The area of individual defects to be repaired must not exceed 10 cm². The permissible number of defects to be repaired is 1 defect per 1 meter of pipe length. Otherwise, the pipe must be recorded.
ISO 21809-1: Specifically for external three-layer extruded polyethylene and polypropylene (3LPE and 3LPP) coatings for steel pipes used in transmission systems in the oil and gas industry.
CSA Z245.21: Specifies external polyethylene anticorrosion coatings for steel pipe used in conveyor systems.
AWWA C215: External polyethylene anti-corrosion coatings suitable for water supply pipes. Although mainly used for water conveyance systems, it has much in common with DIN 30670 in terms of materials and application technology.
We are looking forward to cooperating with you to provide the best quality steel pipe and anti-corrosion coating solutions for your projects. Please feel free to contact us for more product details, we are happy to help you find the best steel pipe option for your needs!