فولاد ضد زنگ (استنلس استیل)مخفف فولاد ضد اسید ضد زنگ است و به گریدهای فولادی که در برابر مواد خورنده ضعیف مانند هوا، بخار، آب، مقاوم بوده و یا دارای خواص ضد زنگ هستند، فولاد ضد زنگ می گویند.
عبارت "فولاد ضد زنگ"به سادگی به یک نوع فولاد ضد زنگ اشاره نمی کند، بلکه به بیش از صد نوع فولاد ضد زنگ صنعتی اشاره دارد که هر کدام در زمینه کاربرد خاص خود عملکرد خوبی دارند.
همه آنها حاوی 17 تا 22 درصد کروم هستند و گریدهای بهتر فولاد نیز حاوی نیکل هستند.افزودن مولیبدن می تواند باعث بهبود بیشتر خوردگی اتمسفر، به ویژه مقاومت در برابر خوردگی در اتمسفرهای حاوی کلرید شود.
一.طبقه بندی فولاد ضد زنگ
1. فولاد ضد زنگ و فولاد مقاوم در برابر اسید چیست؟
پاسخ: فولاد ضد زنگ مخفف فولاد ضد اسید ضد زنگ است که در برابر مواد خورنده ضعیف مانند هوا، بخار، آب یا دارای فولاد ضد زنگ مقاوم است.فولادهای خورده شده فولادهای مقاوم در برابر اسید نامیده می شوند.
به دلیل تفاوت در ترکیب شیمیایی این دو، مقاومت آنها در برابر خوردگی متفاوت است.فولاد ضد زنگ معمولی معمولاً در برابر خوردگی متوسط شیمیایی مقاوم نیست، در حالی که فولاد مقاوم در برابر اسید به طور کلی ضد زنگ است.
2. چگونه فولاد ضد زنگ را طبقه بندی کنیم؟
پاسخ: با توجه به وضعیت سازمانی، می توان آن را به فولاد مارتنزیتی، فولاد فریتی، فولاد آستنیتی، فولاد زنگ نزن آستنیتی-فریتی (دوبلکس) و فولاد زنگ نزن سخت کننده بارشی تقسیم کرد.
(1) فولاد مارتنزیتی: استحکام بالا، اما انعطاف پذیری و جوش پذیری ضعیف.
گریدهای رایج فولاد ضد زنگ مارتنزیتی 1Cr13، 3Cr13 و غیره است، به دلیل محتوای کربن بالا، دارای استحکام، سختی و مقاومت در برابر سایش بالا است، اما مقاومت در برابر خوردگی کمی ضعیف است و برای خواص مکانیکی بالا استفاده می شود. مقاومت در برابر خوردگی.برخی از قطعات عمومی مورد نیاز است، مانند فنرها، پره های توربین بخار، شیرهای پرس هیدرولیک و غیره.
این نوع فولاد پس از کوئنچ و تمپر مورد استفاده قرار می گیرد و پس از آهنگری و مهر زنی نیاز به بازپخت می باشد.
(2) فولاد فریتی: 15٪ تا 30٪ کروم.مقاومت به خوردگی، چقرمگی و جوش پذیری آن با افزایش محتوای کروم افزایش می یابد و مقاومت آن در برابر خوردگی تنش کلرید بهتر از سایر انواع فولاد ضد زنگ مانند Crl7، Cr17Mo2Ti، Cr25، Cr25Mo3Ti، Cr28 و غیره است.
به دلیل محتوای کروم بالا، مقاومت در برابر خوردگی و مقاومت در برابر اکسیداسیون نسبتاً خوب است، اما خواص مکانیکی و خواص فرآیندی آن ضعیف است.بیشتر برای سازه های مقاوم در برابر اسید با تنش کم و به عنوان فولاد ضد اکسیداسیون استفاده می شود.
این نوع فولاد می تواند در برابر خوردگی اتمسفر، اسید نیتریک و محلول نمک مقاومت کند و دارای ویژگی های مقاومت در برابر اکسیداسیون در دمای بالا و ضریب انبساط حرارتی کوچک است.در تجهیزات کارخانه های تولید مواد غذایی و اسید نیتریک استفاده می شود و همچنین می توان از آن برای ساخت قطعاتی که در دمای بالا کار می کنند مانند قطعات توربین گاز و غیره استفاده کرد.
(3) فولاد آستنیتی: حاوی بیش از 18٪ کروم است و همچنین حاوی حدود 8٪ نیکل و مقدار کمی مولیبدن، تیتانیوم، نیتروژن و سایر عناصر است.عملکرد کلی خوب، مقاوم در برابر خوردگی توسط رسانه های مختلف.
به طور کلی، تصفیه محلول اتخاذ می شود، یعنی فولاد تا دمای 1050-1150 درجه سانتیگراد گرم می شود و سپس با آب یا هوا خنک می شود تا یک ساختار آستنیتی تک فاز به دست آید.
(4) فولاد زنگ نزن آستنیتی-فریتی (دوبلکس): دارای مزایای هر دو فولاد زنگ نزن آستنیتی و فریتی است و دارای فوق پلاستیک است.آستنیت و فریت هر کدام حدود نیمی از فولاد ضد زنگ را تشکیل می دهند.
در مورد محتوای کم C، محتوای کروم 18 تا 28 درصد و میزان نیکل 3 تا 10 درصد است.برخی از فولادها همچنین حاوی عناصر آلیاژی مانند Mo، Cu، Si، Nb، Ti و N هستند.
این نوع فولاد دارای خصوصیات فولادهای زنگ نزن آستنیتی و فریتی است.در مقایسه با فریت، دارای انعطاف پذیری و چقرمگی بالاتر، بدون شکنندگی دمای اتاق، بهبود قابل توجهی مقاومت در برابر خوردگی بین دانه ای و عملکرد جوشکاری است، در حالی که آهن را حفظ می کند. .
در مقایسه با فولاد زنگ نزن آستنیتی، استحکام بالایی دارد و مقاومت قابل توجهی در برابر خوردگی بین دانه ای و خوردگی تنش کلرید بهبود یافته است.فولاد ضد زنگ دوبلکس دارای مقاومت بسیار خوبی در برابر خوردگی حفره ای است و همچنین یک فولاد ضد زنگ کم مصرف است.
(5) فولاد ضد زنگ سخت شدن بارش: ماتریس آستنیت یا مارتنزیت است و نمرات رایج فولاد ضد زنگ سخت شدن بارش 04Cr13Ni8Mo2Al و غیره است.این یک فولاد ضد زنگ است که می تواند با سخت شدن بارندگی (همچنین به عنوان سخت شدن سن شناخته می شود) سخت شود (تقویت شود).
با توجه به ترکیب، به فولاد ضد زنگ کروم، فولاد ضد زنگ کروم نیکل و فولاد ضد زنگ نیتروژن کروم منگنز تقسیم می شود.
(1) فولاد ضد زنگ کروم دارای مقاومت خاصی در برابر خوردگی (اسید اکسید کننده، اسید آلی، کاویتاسیون)، مقاومت در برابر حرارت و مقاومت در برابر سایش است و به طور کلی به عنوان مواد تجهیزاتی برای نیروگاه ها، مواد شیمیایی و نفت استفاده می شود.با این حال، جوش پذیری آن ضعیف است و باید به فرآیند جوشکاری و شرایط عملیات حرارتی توجه شود.
(2) در طول جوشکاری، فولاد ضد زنگ کروم نیکل تحت حرارت مکرر قرار می گیرد تا کاربیدها را رسوب دهد، که مقاومت در برابر خوردگی و خواص مکانیکی را کاهش می دهد.
(3) استحکام، شکل پذیری، چقرمگی، شکل پذیری، جوش پذیری، مقاومت در برابر سایش و مقاومت در برابر خوردگی فولاد ضد زنگ کروم-منگنز خوب است.
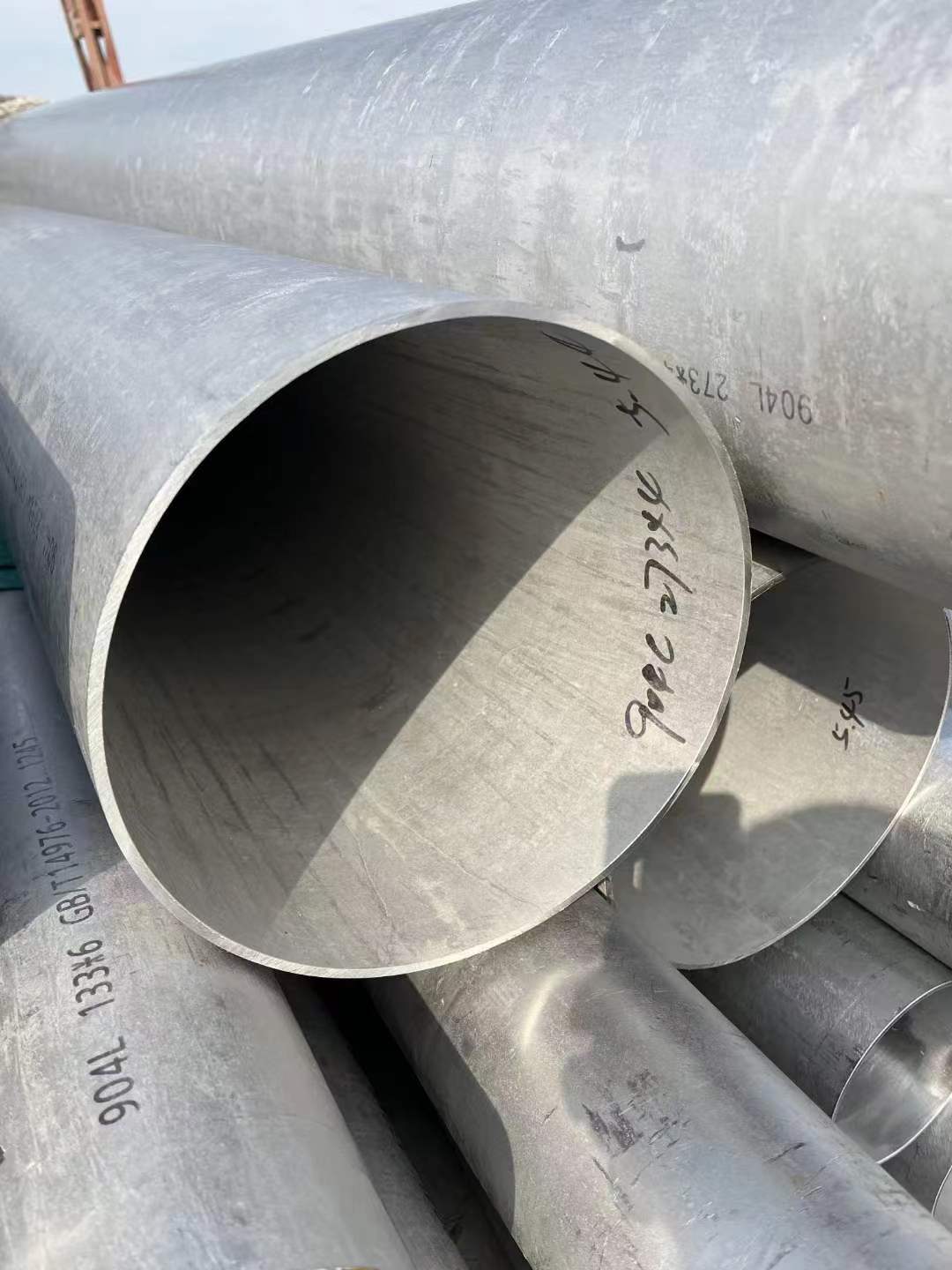
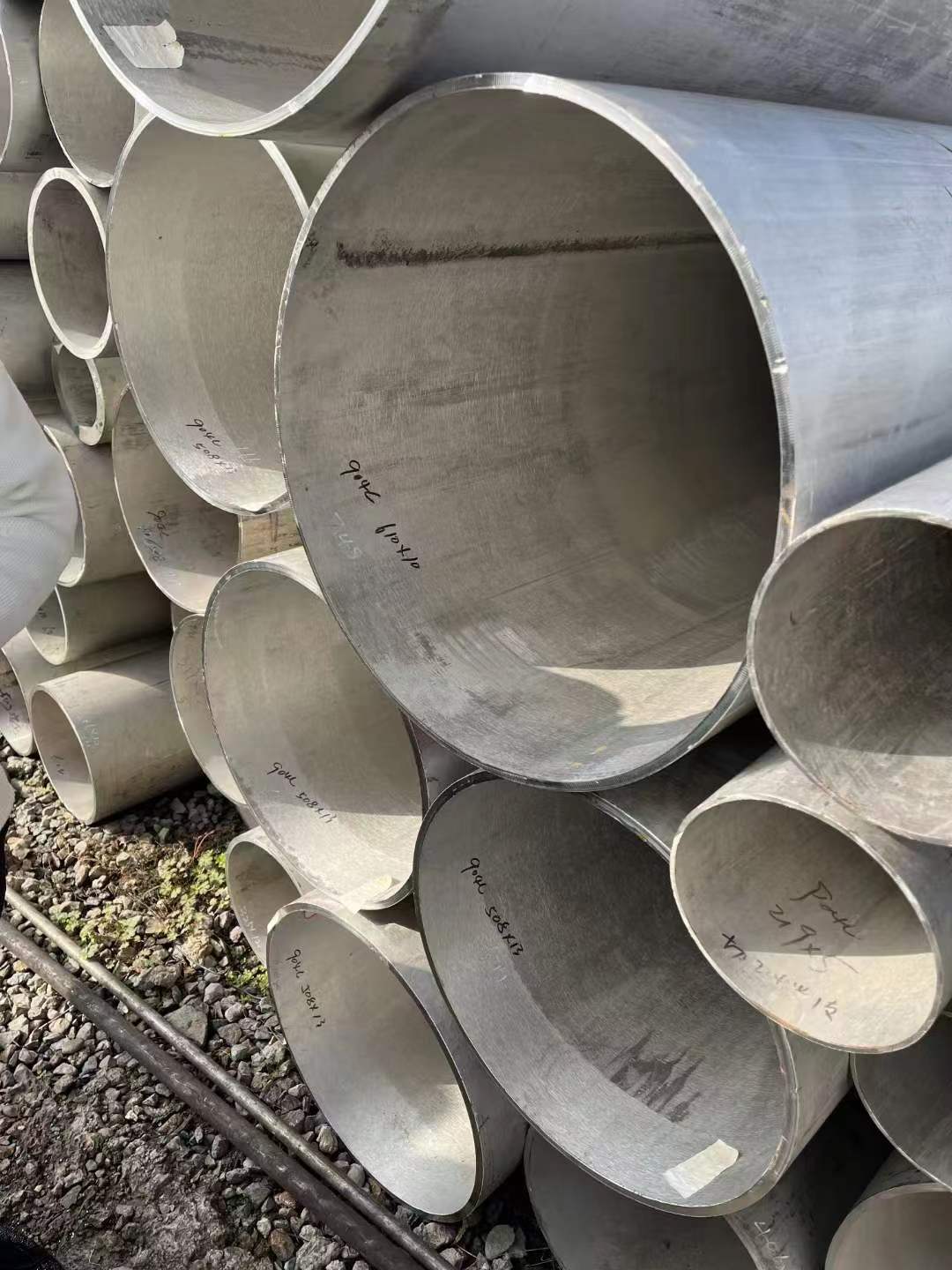
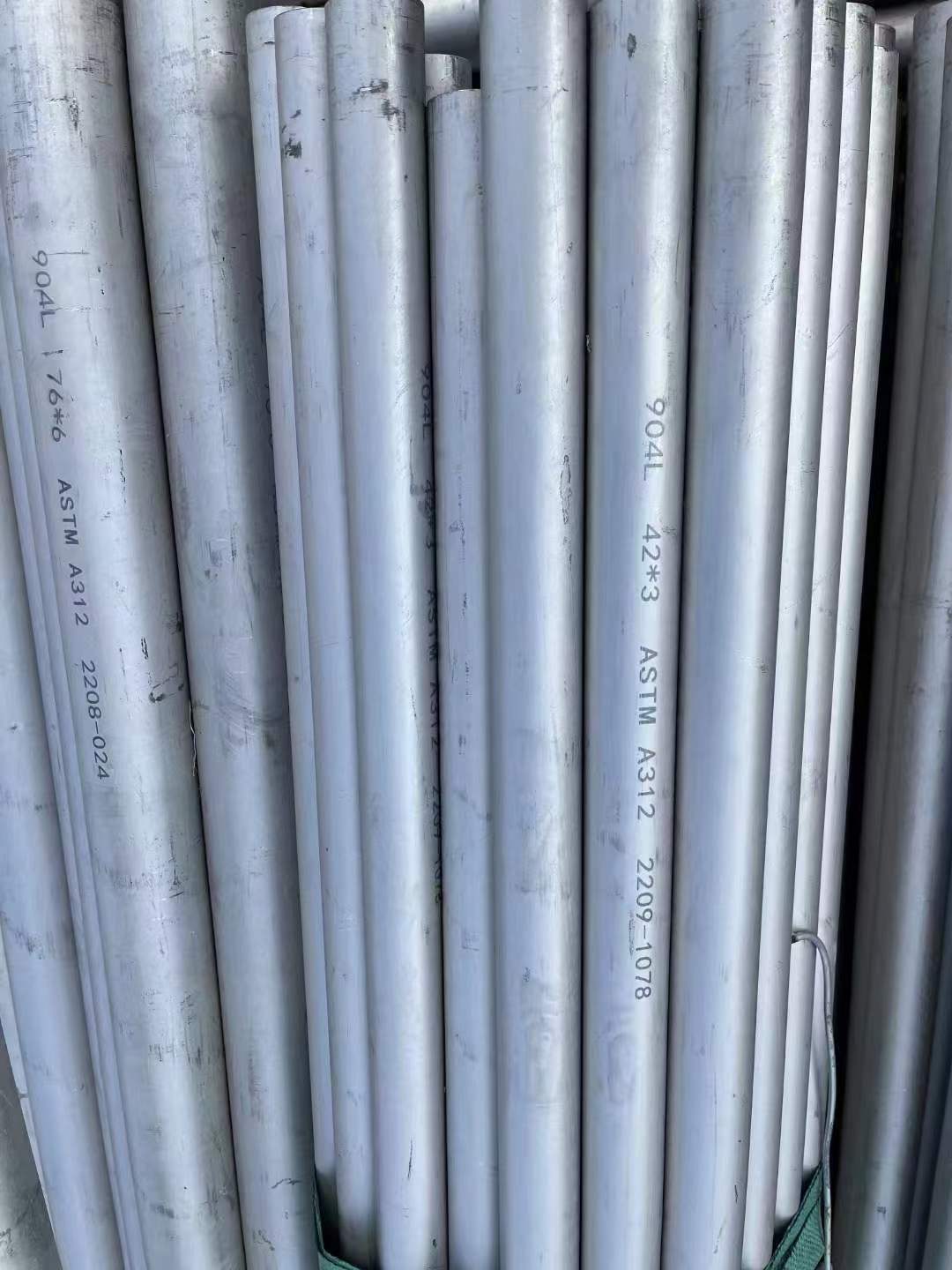
二مشکلات سخت در جوشکاری فولاد ضد زنگ و مقدمه ای برای استفاده از مواد و تجهیزات
1. چرا جوشکاری فولاد ضد زنگ دشوار است؟
پاسخ: (1) حساسیت حرارتی فولاد ضد زنگ نسبتاً قوی است و زمان اقامت در محدوده دمایی 450-850 درجه سانتیگراد کمی طولانی تر است و مقاومت در برابر خوردگی ناحیه جوش و گرما به طور جدی کاهش می یابد.
(2) مستعد ترک های حرارتی؛
(3) حفاظت ضعیف و اکسیداسیون شدید درجه حرارت بالا؛
(4) ضریب انبساط خطی بزرگ است و ایجاد تغییر شکل جوش بزرگ آسان است.
2. برای جوشکاری فولاد زنگ نزن آستنیتی چه اقدامات فنی موثری می توان انجام داد؟
پاسخ: (1) مواد جوشکاری را با توجه به ترکیب شیمیایی فلز پایه به شدت انتخاب کنید.
(2) جوشکاری سریع با جریان کم، انرژی خط کوچک ورودی گرما را کاهش می دهد.
(3) سیم جوش با قطر نازک، میله جوش، بدون نوسان، جوش چند لایه چند پاس؛
(4) خنک کردن اجباری درز جوش و منطقه متاثر از حرارت برای کاهش زمان ماند در 450-850 درجه سانتیگراد.
(5) حفاظت از آرگون در پشت جوش TIG.
(6) جوش های در تماس با محیط خورنده در نهایت جوش داده می شوند.
(7) عملیات غیرفعال سازی درز جوش و منطقه متاثر از حرارت.
3. چرا باید سیم و الکترود جوش سری 25-13 را برای جوشکاری فولاد زنگ نزن آستنیتی، فولاد کربنی و فولاد کم آلیاژ (جوشکاری فولاد غیر مشابه) انتخاب کنیم؟
پاسخ: برای جوشکاری اتصالات جوشی فولادی غیر مشابه که فولاد زنگ نزن آستنیتی را با فولاد کربنی و فولاد کم آلیاژ متصل می کند، فلز رسوب جوش باید از سیم جوش سری 25-13 (309، 309L) و میله جوش (آستنیتیک 312، آستنیت 307 و غیره) استفاده کند.
اگر از سایر مواد مصرفی جوش فولاد ضد زنگ استفاده شود، ساختار مارتنزیتی و ترک های سرد روی خط همجوشی در کنار فولاد کربن و فولاد کم آلیاژ ظاهر می شود.
4. چرا سیم های جوش فولاد ضد زنگ جامد از گاز محافظ 98%Ar+2%O2 استفاده می کنند؟
پاسخ: در هنگام جوشکاری MIG سیم فولادی ضدزنگ جامد، اگر از گاز آرگون خالص برای محافظ استفاده شود، کشش سطحی حوضچه مذاب زیاد است و جوش بد شکل میگیرد و شکل جوش «قوز» را نشان میدهد.افزودن 1 تا 2 درصد اکسیژن می تواند کشش سطحی حوضچه مذاب را کاهش دهد و درز جوش صاف و زیبا است.
5. چرا سطح سیم جوش فولاد ضد زنگ جامد جوش MIG سیاه می شود؟چگونه این مسئله را می توان حل کرد؟
پاسخ: سرعت جوشکاری MIG سیم جوش فولادی ضد زنگ جامد نسبتا سریع است (30-60 سانتی متر در دقیقه).هنگامی که نازل گاز محافظ به ناحیه حوضچه مذاب جلو میرود، درز جوش هنوز در حالت دمای بالا قرار دارد که به راحتی توسط هوا اکسید میشود و اکسیدها روی سطح تشکیل میشوند.جوش ها سیاه هستند.روش غیرفعال سازی ترشی می تواند پوست سیاه را از بین ببرد و رنگ سطح اصلی فولاد ضد زنگ را بازگرداند.
6. چرا سیم جوش فولاد ضد زنگ جامد نیاز به استفاده از منبع تغذیه پالسی برای دستیابی به انتقال جت و جوشکاری بدون پاشش دارد؟
پاسخ: هنگامی که سیم فولاد ضد زنگ جامد MIG جوشکاری، سیم جوش φ1.2، زمانی که جریان I ≥ 260 ~ 280A است، انتقال جت می تواند تحقق یابد.قطره انتقال اتصال کوتاه با کمتر از این مقدار است، و پاشش زیاد است، به طور کلی توصیه نمی شود.
تنها با استفاده از منبع تغذیه MIG با پالس، می توان قطرات پالس را از مشخصات کوچک به مشخصات بزرگ (انتخاب مقدار حداقل یا حداکثر با توجه به قطر سیم) بدون پاشش تبدیل کرد.
7. چرا سیم جوش فولادی ضد زنگ با هسته شار به جای منبع تغذیه پالسی توسط گاز CO2 محافظت می شود؟
پاسخ: در حال حاضر سیم جوش فولادی ضد زنگ با هسته شار (مانند 308، 309 و غیره) استفاده می شود، فرمول شار جوش در سیم جوش مطابق با واکنش متالورژی شیمیایی جوشکاری تحت حفاظت گاز CO2 توسعه یافته است، بنابراین به طور کلی ، نیازی به منبع تغذیه جوش قوس الکتریکی نیست (منبع تغذیه با پالس اساساً نیاز به استفاده از گاز مخلوط دارد) ، اگر می خواهید از قبل وارد مرحله انتقال قطره شوید ، می توانید از منبع تغذیه پالسی یا مدل جوشکاری محافظ گاز معمولی نیز استفاده کنید. جوشکاری گاز مخلوط
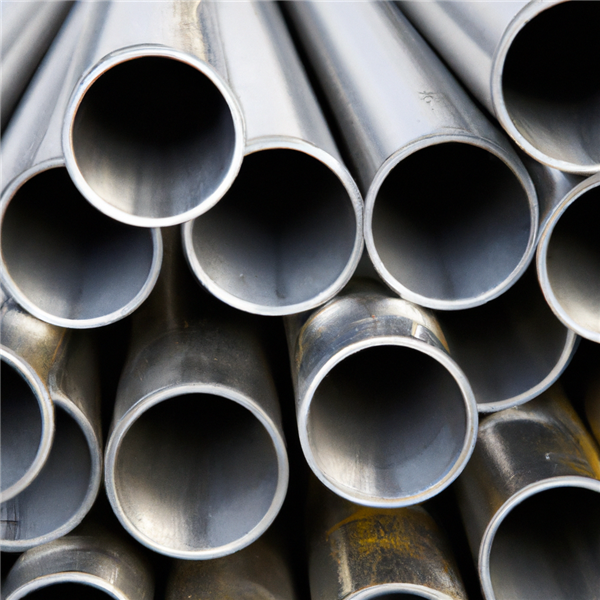
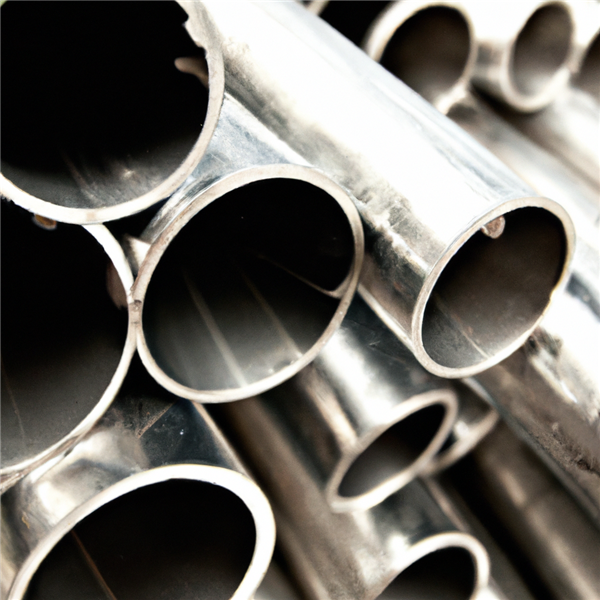
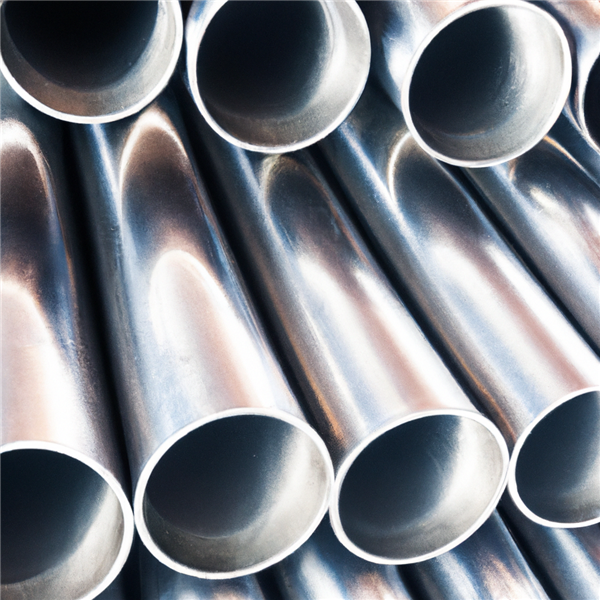
زمان ارسال: مارس-24-2023