Longitudinal Seam Welded Pipe, commonly referred to as LSAW (Longitudinal Submerged Arc Welded) Pipe, is popular across industries due to its superior structural integrity and durability. Among the different types of LSAW pipes, 3PE LSAW steel pipes have received extensive attention from manufacturers and consumers. In this blog post, we will explore the advantages of 3PE LSAW pipe, explain its manufacturing process, and highlight the industry's leading LSAW pipe manufacturers.
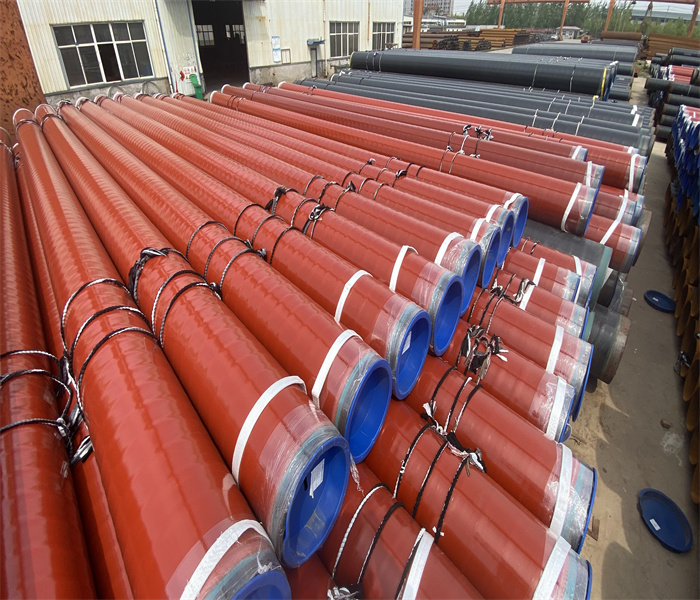
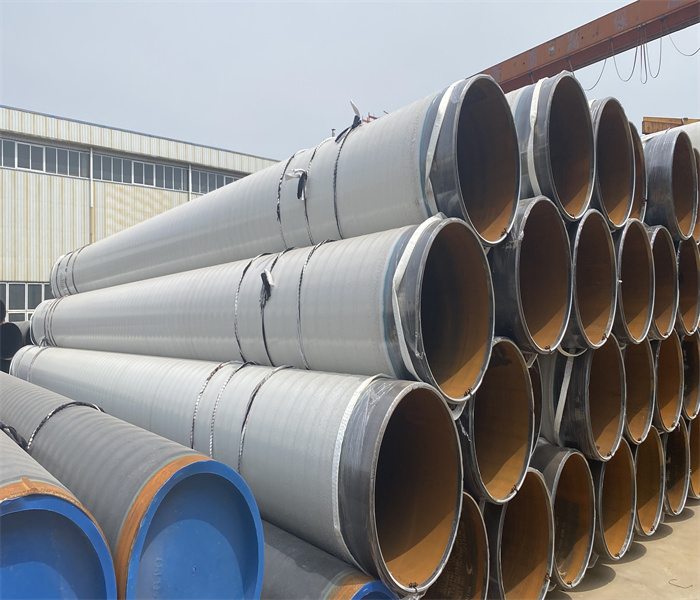
Advantages of 3PE straight seam submerged arc welded steel pipe:
1. Corrosion resistance: 3PE (three-layer polyethylene) coating is one of the outstanding features of 3PE straight seam submerged arc welded steel pipe. The coating has excellent corrosion resistance and is ideal for applications in harsh environments. It acts as a protective barrier, protecting pipes from all kinds of chemicals, moisture and even abrasive substances.
2. Enhanced strength: Since LSAW pipes are longitudinally welded, they have inherently superior strength compared to other types of pipes. The weld seam has excellent toughness and stability, thus enabling 3PE LSAW Welded Steel Pipe to withstand high pressures and extreme temperatures without compromising its structural integrity.
3. Versatility: 3PE LSAW welded steel pipe is widely used in various industries including oil and gas, construction, water treatment and infrastructure development. Due to the ability of these tubes to withstand high internal pressures, they are especially suitable for transporting liquids and gases over long distances.
3PE straight seam submerged arc welded steel pipe manufacturing process:
The production of 3PE LSAW Welded Steel Pipe involves several complex steps. Leading LSAW pipe manufacturers employ well-defined processes to ensure the highest quality standards. Here is a brief overview of the key stages involved:
1. Material preparation: high-quality steel strips are selected, and after strict inspection, they meet the specified mechanical and chemical properties. The strips are then cut to size.
2. Form welding: bend the cut steel strip into the required shape to form a cylindrical shell. Subsequently, the edges of the shell are continuously welded using the LSAW technique, in which a submerged arc welding process is employed.
3. 3PE coating application: After welding, thoroughly clean the outer surface of the LSAW pipe to remove any impurities. Three coats of polyethylene are then applied, including an initial coat of epoxy powder, an adhesive layer and a final layer of colored polyethylene. This coating ensures maximum corrosion resistance.
in conclusion:
In today's fast-paced world, industries require durable and reliable piping solutions, and 3PE LSAW Welded Steel Pipe shines as a valuable option. With their corrosion resistance, increased strength and versatility, they have become an indispensable choice in various industries.
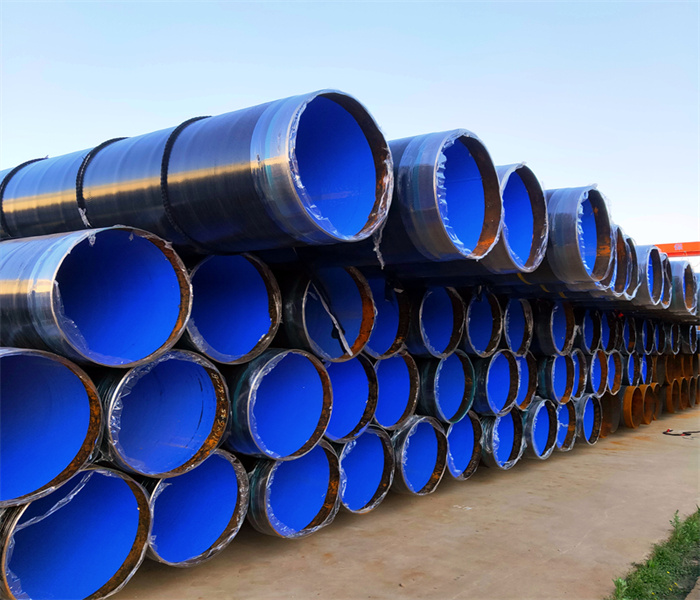
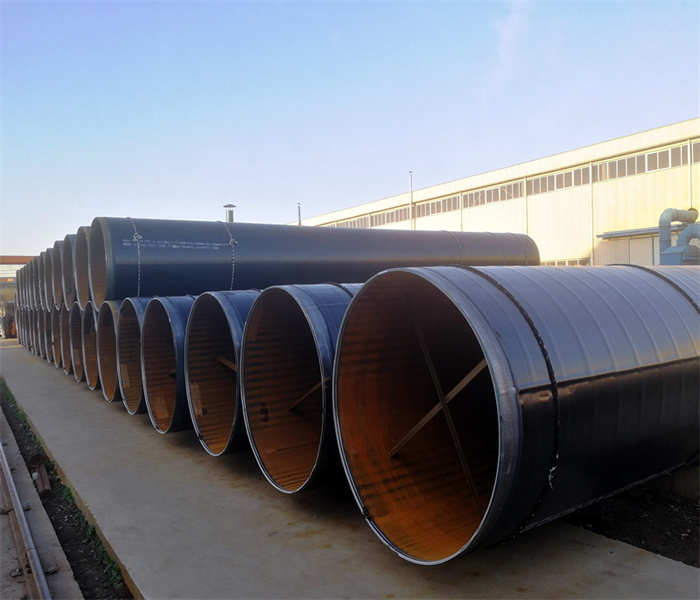
Post time: Aug-28-2023