The most common welding methods used in the fabrication of large-diameter pipelines carrying fluids such as natural gas or oil include double-sided submerged arc welding (DSAW) and longitudinal submerged arc welding (LSAW).
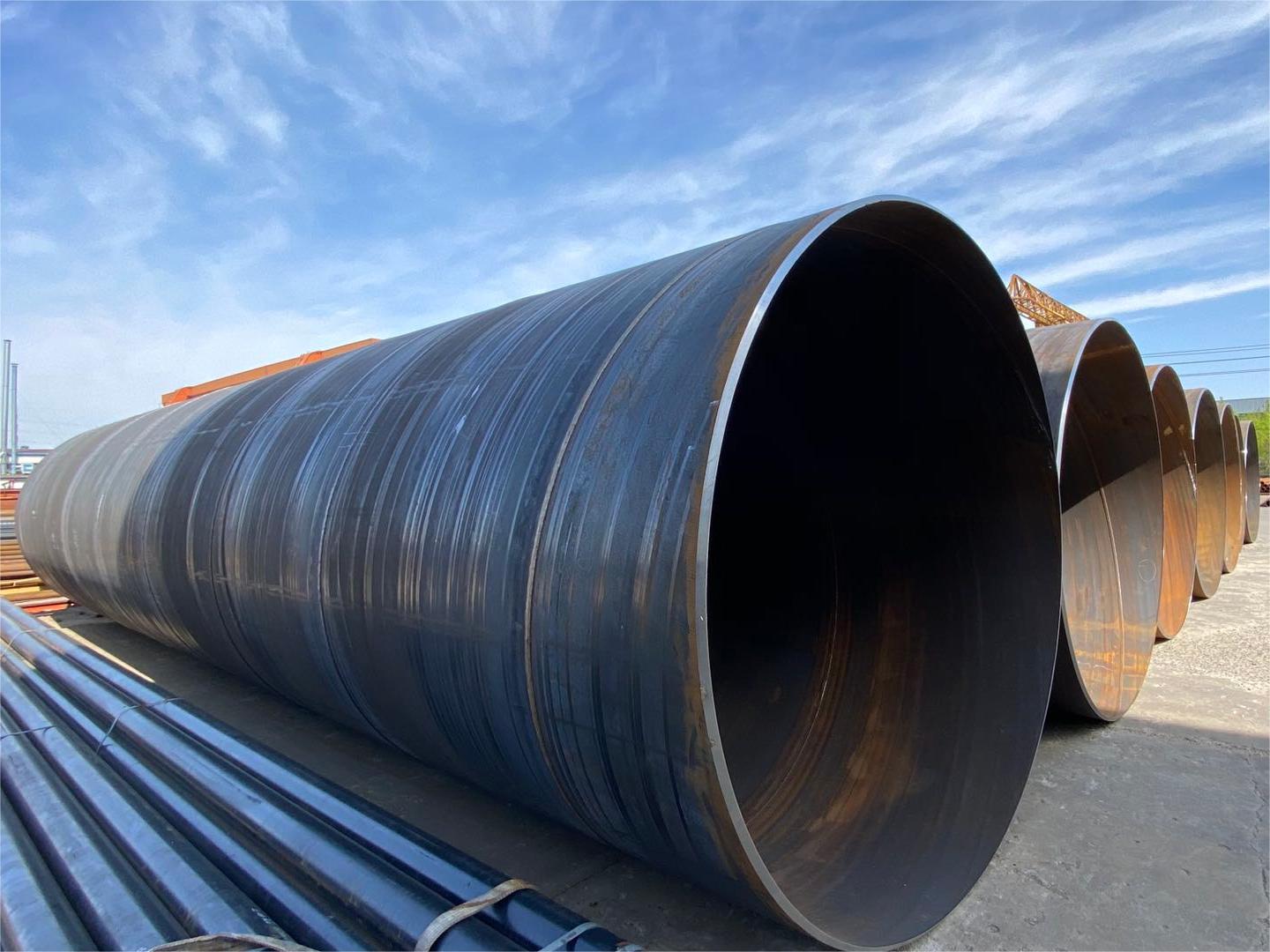
spiral weld
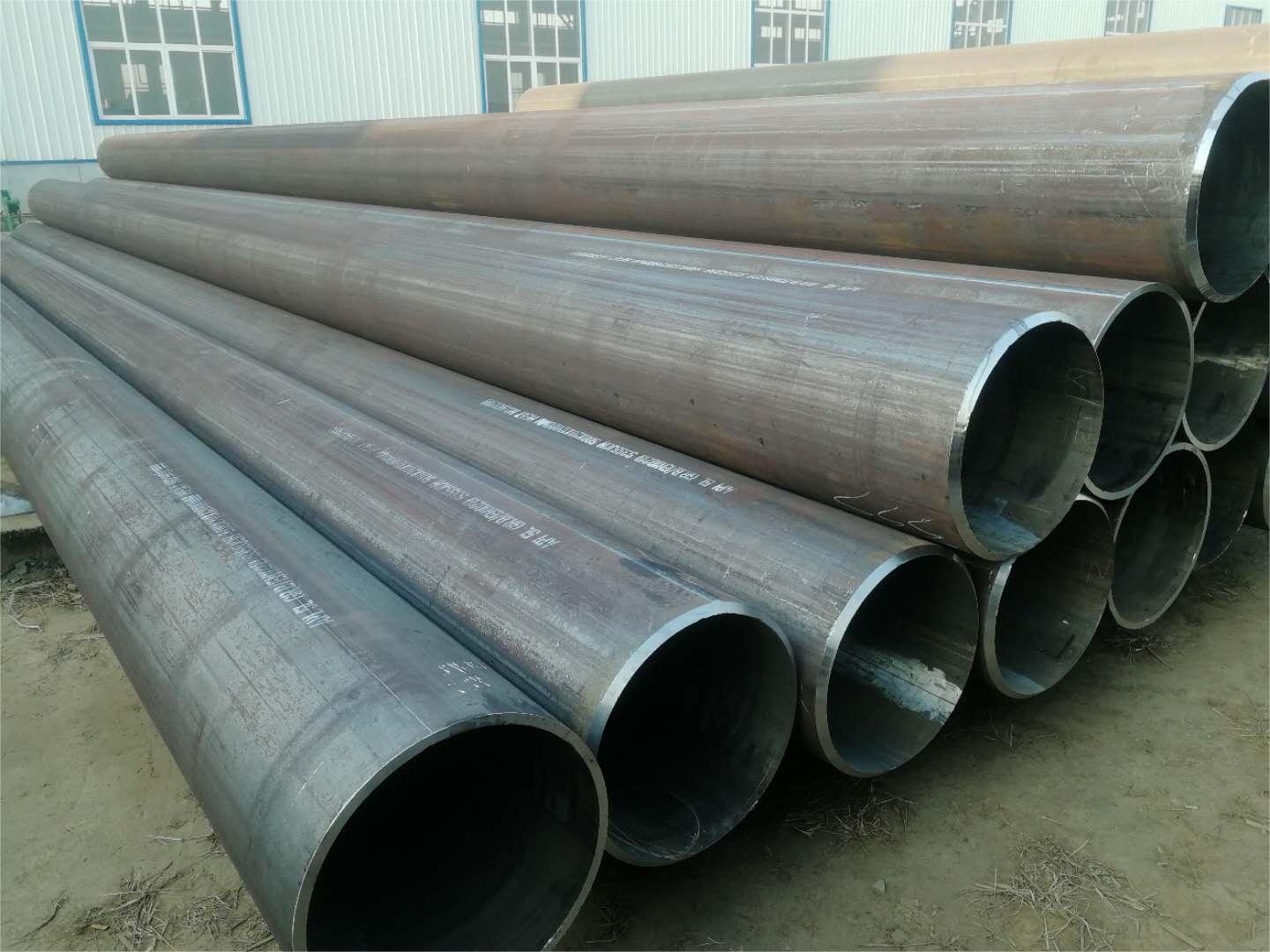
DSAW Steel Pipe:
Longitudinal Welding
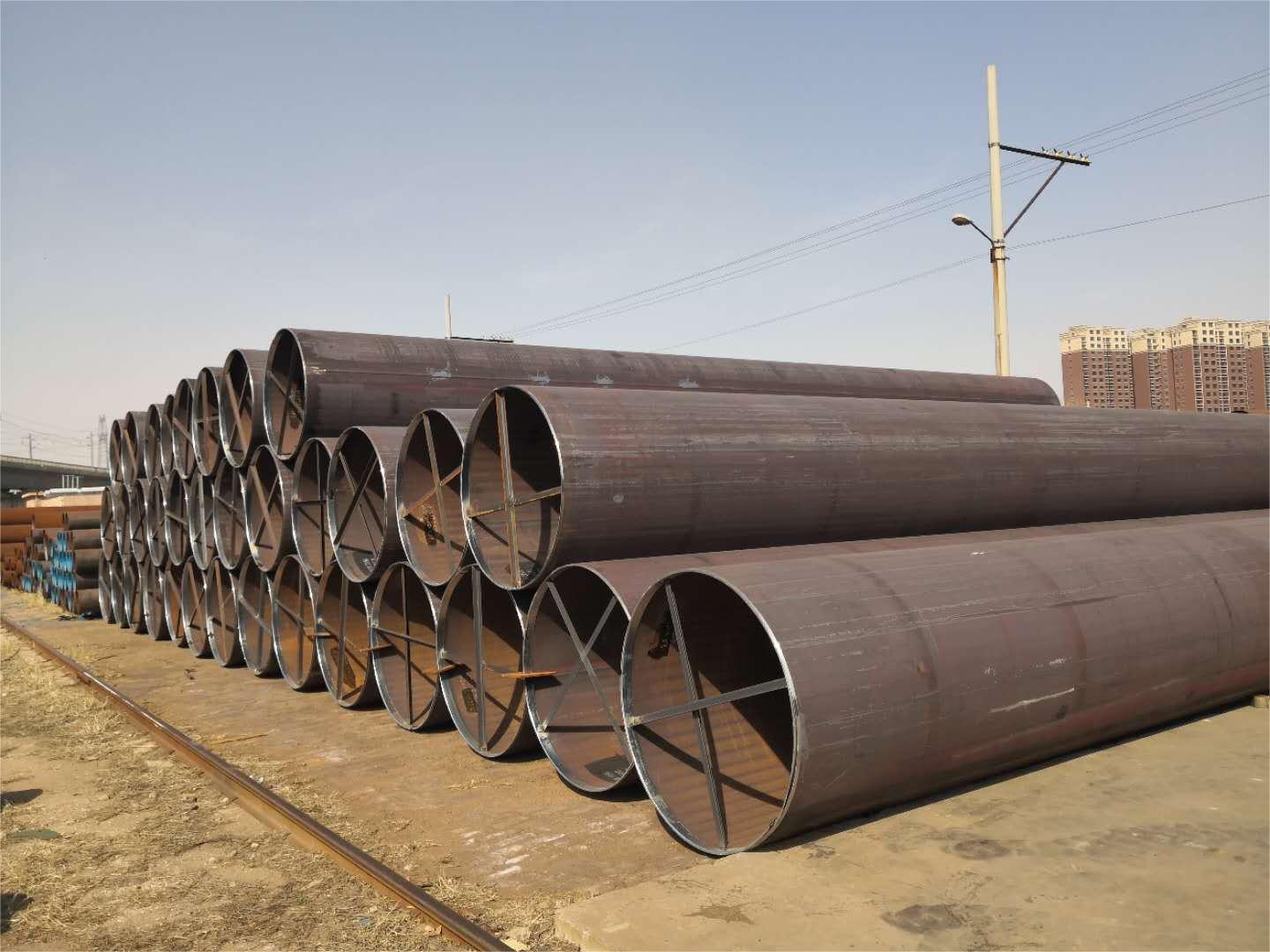
Longitudinal Welding
LSAW is one of the types of DSAW.
DSAW is an acronym for "double-sided submerged arc welding," a term that emphasizes the use of this technique.
LSAW stands for "Longitudinal Submerged Arc Welding," a method characterized by welds that extend along the length of the pipe.
It is important to note that DSAW includes both SSAW (Spiral Submerged Arc Welding) and LSAW types of pipe.
Exploring the similarities and differences between DASW and LSAW is really mainly a comparison between SSAW and LSAW.
Similarities
Welding Technology
Both DSAW and LSAW use the double-sided submerged arc welding (SAW) technique, where welding is performed simultaneously on both sides of the steel to improve the quality and penetration of the weld.
Applications
Widely used in scenarios where high strength and large diameter steel pipes are required, such as oil and gas pipelines.
Weld Seam Appearance
There is a relatively prominent weld seam both inside and outside the steel pipe.
Differences
Type of weld
DSAW: Can be straight (weld along the length of the pipe) or helical (weld wrapped in a helical fashion around the body of the pipe), depending on the use and specifications of the pipe.
LSAW: The weld seam can only be longitudinal, where the steel plate is machined into a tube and welded along its longitudinal length.
Focus on steel pipe applications
DSAW: Since DSAW can be straight or spiral, it is more suitable for a wide range of different pressures and diameters, especially when very long pipes are required spiral DSAW is more suitable.
LSAW: LSAW steel pipes are particularly suitable for urban infrastructure and high-pressure applications such as water and gas transportation.
Pipe Performance
DSAW: Spiral welded pipe does not have the same performance as LSAW in terms of stress tolerance.
LSAW: Because of its manufacturing process steel plate using JCOE and other molding processes, the LSAW steel pipe wall can withstand more uniform mechanical properties.
Cost and Production Efficiency
DSAW: When DSAW pipe is spiral welded it is usually cheaper and faster to produce and is suitable for long-distance pipelines.
LSAW: Straight seam welding, while offering higher quality, is more expensive and slower to produce and is suitable for applications with more stringent quality requirements.
The choice of DSAW or LSAW depends on the specific requirements of the project, including the budget, the pressures the pipe needs to withstand, and the complexity of production and installation. Understanding these key similarities and differences can help make a more appropriate decision for a particular engineering application.
Post time: Apr-24-2024