Longitudinal welded pipes are made by machining steel coils or plates into a pipe shape and welding them along their length. The pipe gets its name from the fact that it is welded in a straight line.
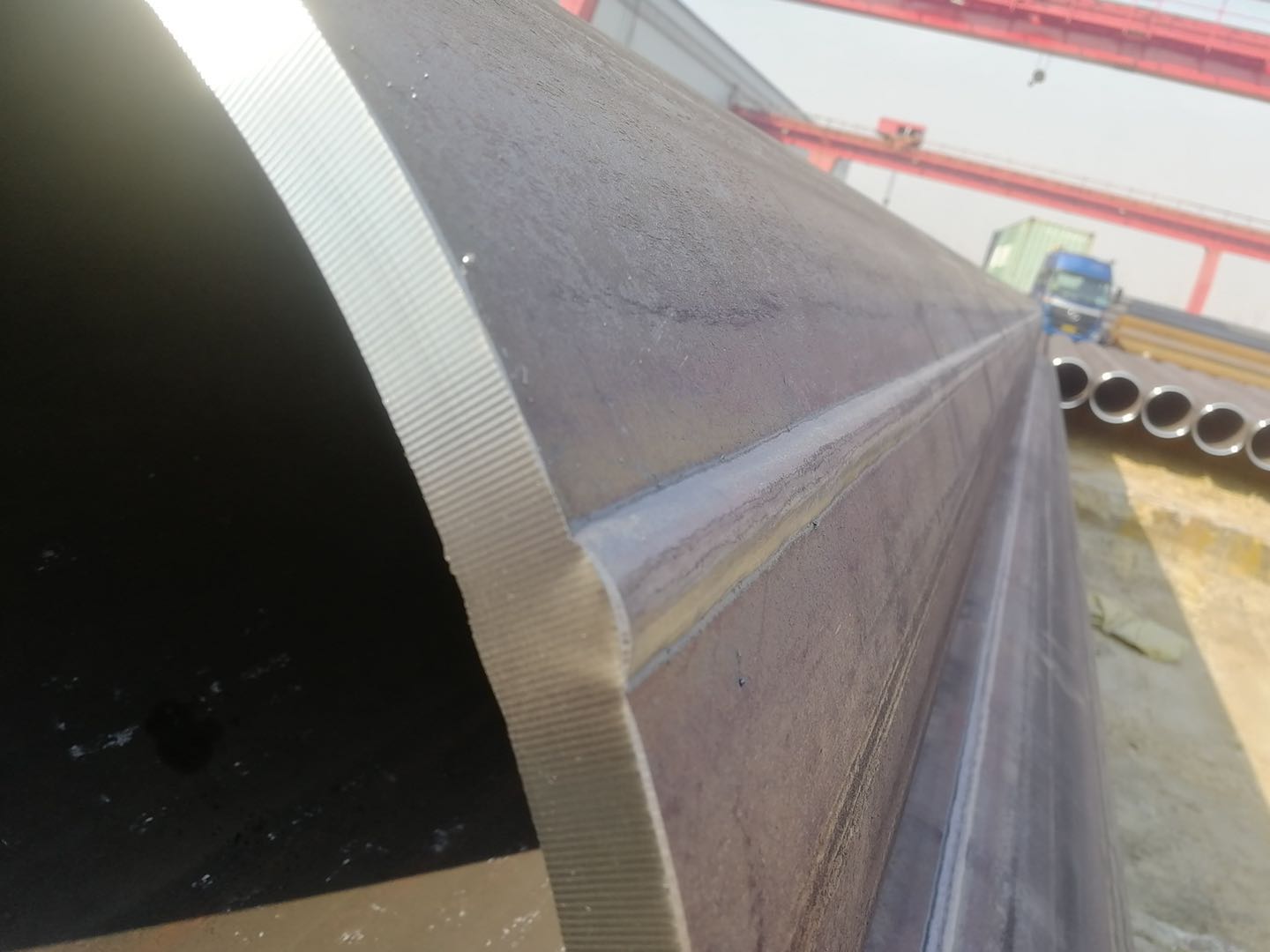
Navigation Buttons
Longitudinal Welded Process and Advantageous Characteristics
ERW and LSAW welded steel pipes are the most common longitudinal seam welding techniques and are widely used.
ERW (Electric Resistance Welding)
Application: Mainly used for the manufacture of small to medium-diameter, thin walled, longitudinally welded steel tubes.
Characteristics: melting of material contact surfaces by resistive heat, heating and pressing of steel edges using high frequency currents.
Advantages: Cost effective, fast production speeds, suitable for high volume production.
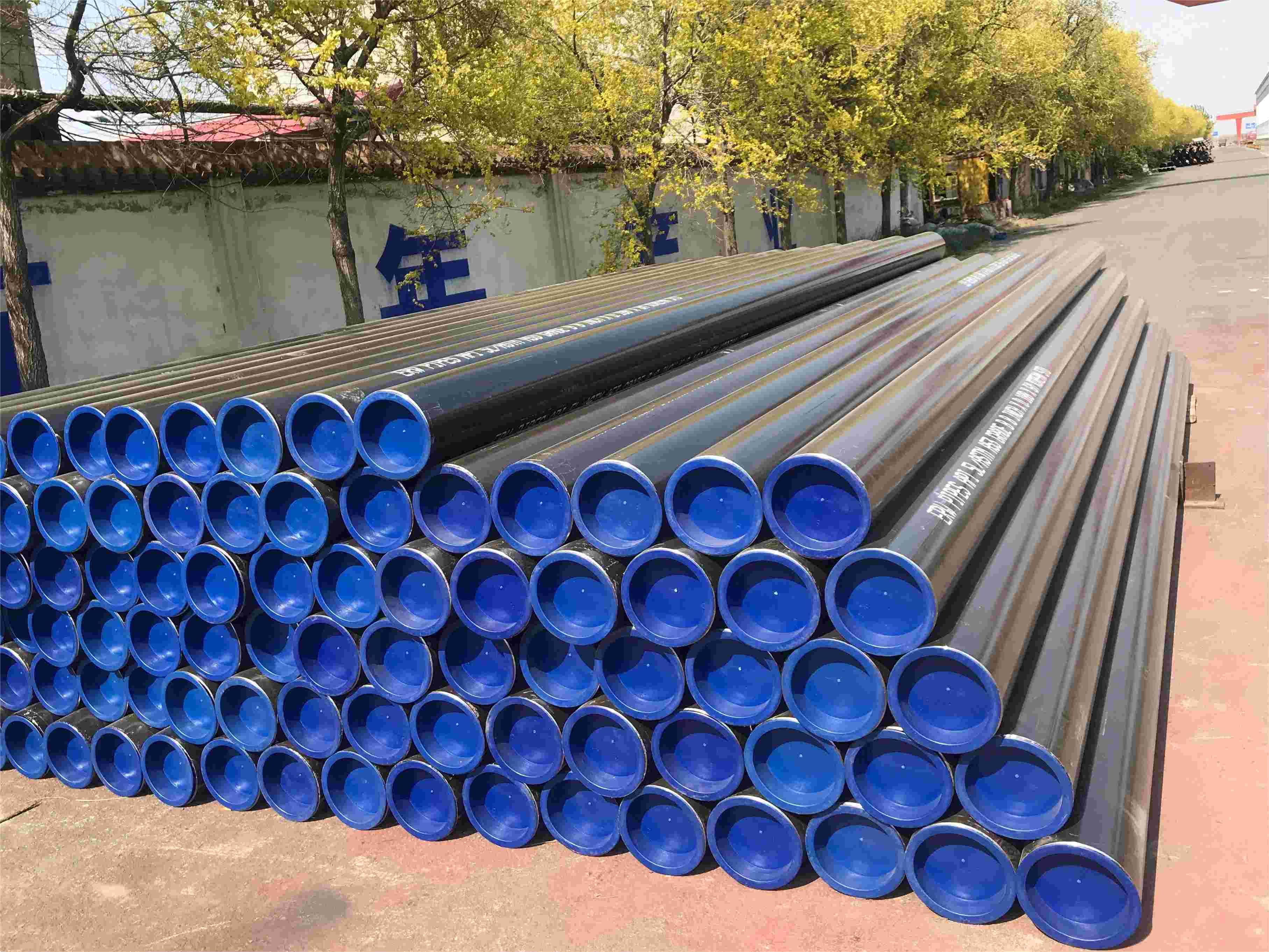
If you know more about ERW, you can click: ERW Round Tube.
LSAW (Longitudinally Submerged Arc Welding)
Application: Suitable for the manufacture of large diameter and thick-walled longitudinal welded steel pipes, commonly used in high-pressure applications such as oil and gas pipelines.
Characteristics: After forming the steel plate into a tube shape, it is welded using submerged arc welding on both the inner and outer simultaneous surfaces of the steel pipe.
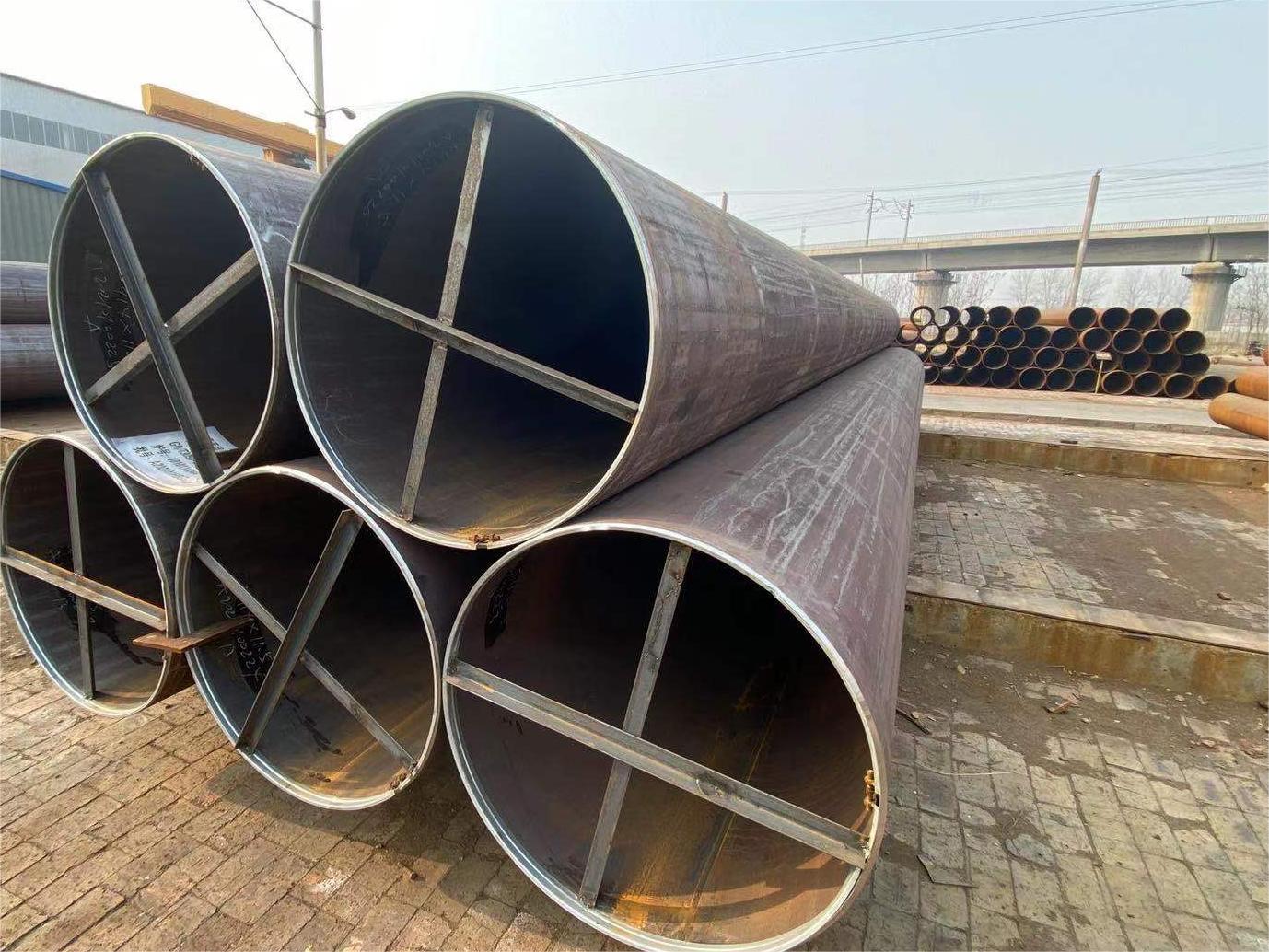
Advantages: Can handle very thick material, good weld quality, and high strength.
If you know more about ERW, you can click: LSAW Pipe Meaning.
Let's take a look at how ERW and LSAW tubes are produced!
ERW Pipe Production Process
Raw material preparation: steel coils of suitable material are selected and pre-treated.
Forming: The steel strip is bent into a tube shape by means of a pressure roller.
Welding: High-frequency current heats the edges of the steel strip and forms the weld through the press rollers.
Weld Cleaning: Cleaning the protruding part of the weld.
Heat treatment: Improvement of weld seam structure and pipe properties.
Cooling and sizing: Cut to specified length as required after cooling.
Inspection: Conduct non-destructive testing and testing of mechanical properties, etc.
LSAW Steel Pipe Production Process
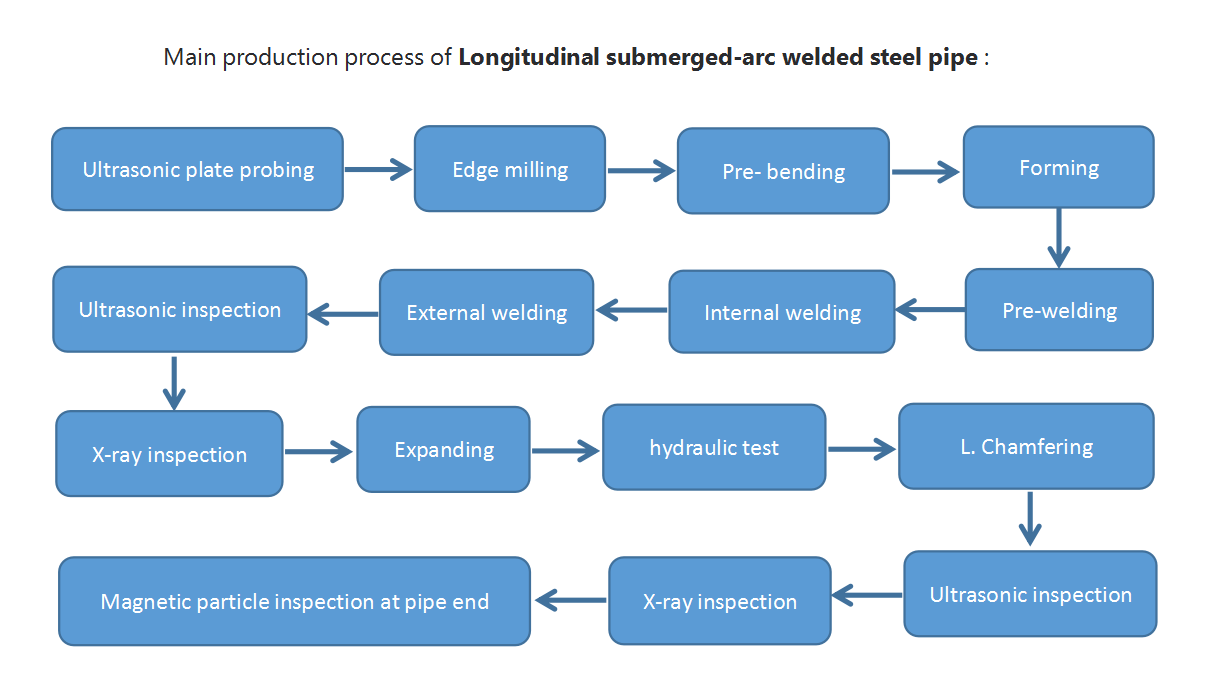
Raw material preparation: select the steel plate of suitable material and carry out pre-treatment.
Forming: Forming using a suitable forming process to bend the steel plate into a tube. The commonly used forming process is JCOE.
Welding: Pre-welding is performed to fix the shape, and then submerged arc welding is used to weld from the inside and outside at the same time.
Straightening: Straightening is performed by a straightening machine
Heat treatment: Normalizing or stress relieving is performed on the welded steel tube.
Expanding: Improve the dimensional accuracy of the steel pipe and reduce mechanical stress.
Inspection: Carry out tests such as hydraulic pressure test flaw detection and mechanical properties.
Executive Standards
Execution Standard of ERW Steel Pipe
API 5L, ASTM A53, ASTM A252, BS EN10210, BS EN10219, JIS G3452, JIS G3454, JIS G3456.
Size Range
Size Range of ERW Longitudinal Welded Steel Pipe
Outer diameter (OD): 20-660 mm.
Wall thickness (WT): 2-20 mm.
Size Range of LSAW Steel Pipe
Outer diameter (OD): 350-1500 mm.
Wall thickness (WT): 8-80 mm.
Longitudinal Welded Steel Pipe Surface Treatment
Interim Protection
For steel pipes that will be stored outdoors or shipped by sea, temporary protective measures are often taken to prevent damage before installation or further processing.
Varnish or Black Paint: Applying a coat of varnish or black paint provides temporary protection against rust, especially in wet or salt spray environments. It is an economical method of temporary protection that is easy to apply and remove.
Wrapping: Wrapped in a tarpaulin, it effectively prevents corrosion caused by environmental factors, especially during prolonged transportation or harsh climatic conditions.
Anti-corrosion
The anti-corrosion layer provides long-term protection for the steel pipe, extending its service life and ensuring its durability and functionality in a variety of environments.
Galvanizing: Coating a layer of zinc on the surface of the steel pipe to prevent corrosion, the zinc layer can be sacrificed to anode protection under the steel.
Epoxy Coating: Commonly used for corrosion protection of internal and external surfaces of steel pipes. It can prevent water and oxygen from coming into contact with the steel surface, thus inhibiting the rusting process.
Polyethylene (PE) Coating: The application of a PE coating to the exterior of steel pipe is commonly used for natural gas and oil pipelines. The coating is chemically resistant, water resistant, and has good mechanical protection properties.
Types of Longitudinal Steel Pipe End Processing
Plain End
Used for welded connections and suitable for field welded applications to allow for a tight fit of the tubing.
Beveled End
A pipe end cut to a beveled surface, usually at an angle of 30°-35°, is used primarily to increase the strength of welded joints.
Threaded End
Pipe ends are machined to internal and external threads for threaded connections that require easy disassembly, such as water and gas piping.
Grooved End
A pipe end machined with an annular groove for mechanical connections is commonly used in fire sprinkler and HVAC systems.
Flanged End
Welded or fixed flanges on pipe ends for large pipes and high-pressure systems that require frequent disassembly.
Longitudinal Welded Steel Pipe Applications
It is mainly used in the two main areas of structural support and conveyor systems.
Structural Support Function
Building frames: Longitudinal steel tubes are used as columns and beams in modern construction, especially in high-rise buildings and large-span structures.
Bridge construction: Longitudinal steel tubes are used as the main load-bearing members of bridges, such as bridge piles and abutments.
Industrial supports and frames: Used in heavy industry, such as petrochemical, manufacturing, and mining facilities, to construct machine supports and safety rails.
Wind Towers: Longitudinal steel tubes are used in the wind power industry to manufacture towers for wind turbines, which require long sections and high strength to withstand wind loads.
Conveyor Systems
Oil and gas pipelines: used to construct oil and gas pipelines, the pipelines usually cover long distances and require good mechanical strength and corrosion resistance.
Water supply and drainage systems: widely used in municipal and industrial water supply and wastewater treatment systems, longitudinal welded steel pipes are widely used for their durability and ability to withstand higher pressures.
Chemical transportation piping: used in chemical plants for the transportation of various chemicals, longitudinal welded steel pipe has good chemical stability to prevent corrosion of the medium.
Subsea applications: Used in pipelines for the development of subsea oil and gas fields, longitudinal welded steel pipes are suitable for use in extreme environments due to their strength and corrosion resistance.
We are a high-quality welded carbon steel pipe manufacturer and supplier from China, and also a seamless steel pipe stockist, offering you a wide range of steel pipe solutions!
Tags: Longitudinal welded, lsaw, erw, suppliers, manufacturers, factories, stockists, companies, wholesale, buy, price, quotation, bulk, for sale, cost.
Post time: Apr-18-2024